La extracción de minerales es una de las actividades más importantes en México. En los yacimientos, las reservas de fluorita son las de mayor pureza y calidad, por lo que su producción es de suma importancia para la industria nacional e internacional. Sus aplicaciones contemplan desde la fabricación de acero hasta la elaboración de refrigerantes
Eréndira Reyes / Bruno Martínez, fotografías
La fluorita es un fluoruro de calcio (CaF2) que pertenece a la clase de los haluros, los cuales se caracterizan por la abundancia de halógenos electronegativos, tales como cloro, bromo, flúor o yodo. Posee un brillo vítreo y un peso específico que oscila entre 3 y 3.2 gramos por centímetro cúbico. Su dureza, según la escala de Mohs, es de 4 y su coloración varía, ya que puede tener tonos azules, púrpuras, verdes, amarillos, entre otros. Presenta exfoliación perfecta y es posible que se clasifique como un material frágil.
También es posible encontrarlo en cristales de hábito cúbico muy bien formados, frecuentemente con maclas de penetración (agrupación simétrica de cristales idénticos). Al calentarse o exponerse a algún tipo de radiación se torna fluorescente y fosforescente, aunque esta característica depende de la composición de la piedra.
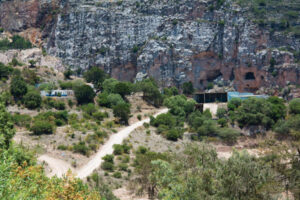
Por otro lado, las impurezas que presenta son minerales como calcita, cuarzo, barita, celestita, sulfuros y fosfatos. A nivel comercial, se clasifica de acuerdo con su calidad y su especificación en grados ácido, metalúrgico y cerámico, por lo que a partir de esta valoración se determina su uso.
Las aplicaciones de la fluorita, en orden de importancia, se enfocan en la producción de ácido fluorhídrico, solución acuosa de fluoruro de hidrógeno, el cual también es un compuesto químico formado por hidrógeno y flúor; se utiliza como catalizador en la química orgánica para la obtención de compuestos químicos orgánicos fluorados, con la finalidad de conseguir criolita artificial, la cual es empleada en la obtención del aluminio, fluoruros inorgánicos, como el hexafluoruro de uranio, y en ocasiones como disolvente.
Además, se emplea para la fabricación de acero, producción de aluminio y refrigerantes. Al agregarle ácido sulfúrico, se descompone en fluoruro de hidrógeno gaseoso y sulfato de calcio, reacción fundamental para producir ácido fluorhídrico, el cual proporciona fluidez a bajas temperaturas. Como se menciona, la calidad del mineral determina su uso y el proceso al que se someterá la materia prima para derivar en productos de enorme importancia para la industria nacional e internacional.
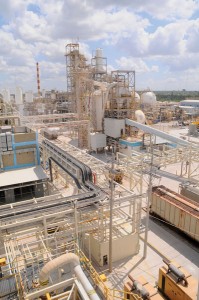
Grado ácido. Es un concentrado muy fino que contiene 97.1 % de fluoruro de calcio (CaF2), aunque presenta impurezas, como óxido de silicio (SiO2) 1.5 %; azufre como sulfuro o en estado libre, que puede hallarse en concentraciones de 0.03 a 0.1 %, además de arsénico (H3AsO4) de 10 a 12 partículas por millón y fósforo promedio (P) entre 100 y 500 partículas por millón. Dentro de los parámetros para su producción, hay una restricción total para plomo, cadmio, berilio, carbonato de calcio y mezclas.
Grado cerámico. Este grado se divide en tres. El primero va desde 85 hasta 96 % de fluoruro de calcio (CAF2), el cual tiene limitantes para impurezas: se debe conservar con una composición menor a 2.5-3.0 % SiO2, 0.12 % de óxido férrico (Fe2O3), caliza muy limitada, plomo (Pb) y sulfato de zinc (ZnSO4). Sólo se permiten en trazas (cantidad minúscula de una sustancia en una mezcla química).
Las otras dos divisiones van de acuerdo con sus aplicaciones, ya que también puede usarse para la fabricación de lentes. Cuando está en su estado más puro, es descolorida y transparente con una textura vidriosa. El color que llega a tomar se debe a las impurezas de la piedra, y en muchas variedades puede ser fluorescente.
A nivel mundial, la explotación de este mineral se concentra en China, México, Mongolia y Rusia. En la República Mexicana, los estados productores de fluorita son San Luis Potosí, con 93 %, y Coahuila, con 7 %, los cuales explotan el mineral y lo comercializan para distintos sectores en México y en el mundo. Los yacimientos en San Luis Potosí contienen cuerpos de grandes dimensiones que se forman por el contacto entre las rocas carbonatadas con las rocas volcánicas terciarias.
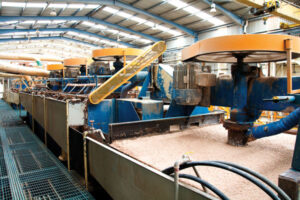
Grado metalúrgico
Contiene un mínimo efectivo de 60 % de fluorita y es posible que contenga impurezas de 0.3 % de sulfuro de hierro (FeS) y 0.5 % de Pb. La concentración de fluoruro de calcio puede oscilar entre 70 y 93 %, con un máximo de 15 % de SiO2. Usualmente se requiere que pase por una malla de entre 1 y 1.5 pulgadas, aunque este manejo dependerá de los requerimientos que establezca el cliente.
El depósito Las Cuevas es uno de los más grandes de alta ley de fluorita y consiste en un grupo de cuerpos masivos encajonados en zonas de contacto, debido a la formación El Doctor y a una brecha riolítica terciaria. El cuerpo de fluorita en sí mismo está brechado con fluorita y caliza, lo que forma clastos: fragmentos de roca que aparecen en sedimentos de menor antigüedad, que en este caso se encuentran incrustados en un cementante de fluorita y calcita.
En cuanto a la ley mineral que posee, varía entre 50 y 98.5 % de CaF2. En lo que respecta a los sedimentos que se ubican en Coahuila, los depósitos con los que cuenta son en su mayoría filones y mantos de reemplazamiento, y presentan una configuración de lentes eslabonados de varias dimensiones.
Es importante mencionar que hay otras localidades que cuentan con presencia de fluorita, como Zacualpan, en el Estado de México; Galeana, en Nuevo León; San Francisco del Oro, en Chihuahua, y en varios lugares del estado de Zacatecas; pero las concentraciones que tienen son menores a las de San Luis Potosí y Coahuila.
Recientemente, Mundo HVAC&R visitó la mina de donde se extrae la materia prima que inicia la cadena de flúor. Como guía del recorrido, el ingeniero Luis Alfredo Esparza mostró el proceso para obtener el ácido fluorhídrico (HF) necesario en la producción de refrigerantes y otros productos.
Mexichem y la cadena de fluorita
La compañía Mexichem tiene la mina de flúor más grande a nivel mundial, lo que la ha posicionado como el mayor productor de fluorita y el segundo productor de ácido fluorhídrico. Debido a esto, su presencia en la economía nacional es indudable, pues su desarrollo se localiza en varios sectores productivos y manufactureros. Desde 2006 representa una sola empresa, situada en una de las regiones con mayor concentración del mineral, pero ha expandido sus plantas y oficinas a lo largo del país y del mundo.
Las dimensiones donde se asienta el yacimiento oscilan entre 700 y 800 metros de longitud, con un ancho de entre 50 y 200 metros, y una profundidad de entre 200 y 680 metros, máximo registrado hasta el momento. La concentración con la que cuenta es diversa, pero oscila entre 60 y 95 %. Donde existe mayor concentración se instalan contactos, ya que de esta manera las áreas se ubican con mayor facilidad.
El yacimiento se encuentra encasillado entre los fenómenos El Doctor, que contiene caliza, y un cuerpo de riolitas. El minado se lleva a cabo por subniveles. En el caso de la visita, se realizó en el nivel cero de los 260 con los que cuenta. Para ubicarse dentro de la mina ha sido necesaria la instalación de brocales alrededor, los cuales sirven como apoyo a los trabajadores. La política bajo la que se rige la compañía es que por cada tonelada que se extrae, se provee al yacimiento con dos más. Esto permite que el impacto ambiental sea menor.
El proceso productivo para obtener fluorita requiere la puesta en marcha de diversas etapas:
1) Extracción. Los depósitos se explotan por el método de tumbe de subniveles, el cual puede hacerse de tres formas: con herramientas especiales, maquinaría o por medio de explosivos. En este caso, se utiliza un método de voladuras similar al que se emplea en rocas ornamentales, como el mármol, pues al ser un mineral de poca dureza no requiere gran cantidad de explosivos.
Varios factores determinan el tipo de extracción y los pasos por seguir en la mina; por ejemplo, en el lugar donde se llevó a cabo el recorrido, se hace una extracción en rodajes abiertos porque la subsidencia del lugar lo permite, factor determinante en el trabajo de minas subterráneas. Cada voladura que se mina recoge un aproximado de 1 mil 850 toneladas, que al día genera una producción de 5 mil 500 toneladas para la compañía.
El siguiente proceso que se realiza en esta etapa es el de toneleo, que se lleva a cabo con equipo electrohidráulico, pues se monta una máquina perforadora que hace una barrenación con ayuda de agua. Después de terminar el barrenado de la voladura, se carga el mineral extraído en camiones con una capacidad de 40 toneladas para llevarlo a través de galerías y rampas al proceso de triturado primario, donde pasará de un tamaño de 48 pulgadas a una dimensión más manejable de 8 pulgadas.
La extracción del mineral es por medio de cruceros que se localizan en el nivel inferior a los subniveles y por los que se lleva a cabo el acarreo del mineral. Este tipo de cruceros tiene un movimiento simétrico al viajar, debido a que, cuando se acarrea el mineral hacia el exterior y se vacía, el siguiente crucero ya lleva más material, lo que acelera el proceso y lo mantiene a una velocidad constante.
2) Clasificación. Tras de la primera trituración, pasa a la etapa de clasificación, en la cual, mediante un sistema de cribado, se separa el mineral grado metalúrgico del fino, pues éstos se someterán a procesos diferentes.
En el primer caso, debe ser igual o mayor a ¾ de pulgada, mientras que el material fino es el menor a esta dimensión. Si es material grado metalúrgico, normalmente se envía a almacén para después tratarlo, según las necesidades del cliente; en cambio, en el segundo caso se traslada a la planta de beneficio para recibir otro proceso. Esta clasificación se hace manualmente y se sirve de distintos tamaños estandarizados.
Los clientes normalmente piden tres productos: el prototípico, que va de -2 pulgadas a +¼ y tiene una concentración química de 85 a 90 % de fluoruro (HF); otro que emplea el granzón, material con características similares al prototípico, que sólo presenta diferencias en el tamaño, pues va de -¼ a +¾ de pulgada, y el pisite, con una dimensión de -¾ a +¼ que, al igual que los otros tipos, maneja una calidad química de entre 85 y 90 % de HF.
3) Molienda. Este procedimiento se lleva a cabo por medio de molinos de bolas. Da como resultado una pulpa con tamaño de grano de 325 mallas como producto final.
4) Acondicionamiento. En esta etapa se adicionan reactivos y depresores. Los primeros servirán para separar a la molécula de fluorita de los demás elementos, que normalmente son compuestos de carbonato de calcio y sílice, los cuales son deprimidos para facilitar la recolección de partículas de fluorita liberadas.
5) Flotación. La pulpa que resulta del proceso anterior se envía al banco de celdas de flotación para su concentración, donde se le inyecta aire para generar burbujas que, junto con los reactivos químicos suministrados, logran un material con una concentración de 97.3 %.
6) Deshidratación. El producto debe pasar por un tanque espesador que moverá las partículas sólidas a otro inferior, donde se concentra toda la humedad y se elimina para que finalmente quede una concentración de 10 % de humedad como máximo.
7) Muestreo. Para entregar a los clientes el concentrado de fluorita, se evalúa, a través de muestreo y análisis químico-físico, el contenido de los principales elementos que debe contener, con el objetivo de garantizar a los clientes que el producto que reciben es de buena calidad.
8) Embarque. La mayoría de los productos finales se envía a la industria química y siderúrgica a granel por medio de tráileres, barcos o ferrocarriles. También se pueden trasladar en supersacos a la industria de la soldadura.
La fluorita es un elemento que se encuentra en la gasolina, en combustibles nucleares, circuitos integrados y cremas dentales. Se emplea en la fabricación de acero, vidrio, cerámica y cemento; además, puede derivar en HF, químico que se utiliza en la fabricación de gases refrigerantes para aire acondicionado, refrigeradores y congeladores.