En diversas industrias y actividades productivas, los filtros de alta eficiencia se emplean con fines de control de calidad y prevención de la contaminación de productos. Garantizar que capturen el tipo de partículas previsto y con la eficacia necesaria exige que se sometan a diversas pruebas que evalúan su grado de efectividad y aseguran que el trabajo requerido será cumplido.
Édgar Uribe
Para comprobar la eficiencia en los filtros de partículas de alta eficiencia existen diversos parámetros, los cuales varían de acuerdo con la zona geográfica, con las políticas sanitarias y con los requerimientos de cada instalación específica.
En concreto, los filtros de alta eficiencia presentan exigencias mayores en la captura de partículas por las actividades de las áreas para las que fueron creados. En la región europea, existen estándares que se deben considerar.
En primer lugar, se tiene que los filtros de alta eficiencia que aplican en el viejo continente son el del Environmental Protection Agency (EPA), el High Efficiency Particle Arresting (HEPA) y por último el Ultra Low Particle Air (ULPA).
El estándar Europeo EN 1822:2009, para filtros de aire de alta eficiencia EPA, HEPA y ULPA, define el método para hacer las pruebas de eficiencia basado en el conteo de partículas, utilizando un aerosol líquido que permite la clasificación sistemática de acuerdo con su eficiencia.
Los filtros HEPA y ULPA son usados como filtros de alta calidad para la separación de aerosoles, polvos tóxicos, virus y bacterias, y son también empleados para aplicaciones con los requerimientos más específicos de pureza del aire en tecnología de cuartos limpios. Estos filtros son sujetos a pruebas y clasificados de acuerdo con el estándar EN 1822:2009.
El estándar europeo comprende las siguientes partes:
EN 1822-1:2009
Clasificación, prueba de desempeño y calificación
EN 1822-2:2009
Producción de aerosol, equipo de medición y de conteo de partículas estadístico
EN 1822-3:2009
Prueba de la malla plana de filtración
EN 1822-4:2009
Determinar fugas en las mallas filtrantes (método de escaneo)
EN 1822-5:2009
Determinar la eficiencia de la malla filtrante
Tabla 1 | |||||
Grupo | Clase de filtro | Valor integral | Penetración | Valor local | Penetración |
Eficiencia en la filtración | Eficiencia en la filtración | ||||
EPA | E10 | 85% | 15% | – | – |
E11 | 95% | 5% | – | – | |
E12 | 99.50% | 0.50% | – | – | |
HEPA | H13 | 99.95% | 0.05% | 99.75% | 0.25% |
H14 | 100.00% | 0.01% | 99.98% | 0.03% | |
ULPA | U15 | 100.00% | 0.00% | 100.00% | 0.00% |
U16 | 100.00% | 0.00% | 100.00% | 0.00% | |
U17 | 100.00% | 0.00% | 100.00% | 0.00% |
EN 1822-1:2009. El inicio de este estándar contiene la clasificación, prueba de desempeño, prueba de los filtros y la calificación de los filtros EPA, HEPA y ULPA. Con base en los valores determinados para la eficiencia individual y la eficiencia global, el filtro es clasificado en diferentes tipos de modelos, como se muestra en la Tabla 1.
EN 1822-2:2009. La segunda parte de este estándar describe el equipo de medición y los generadores de aerosol usados dentro del rango de esta prueba. En adición, con respecto al conteo de partículas, éste especifica la base estadística para la evaluación de cada conteo con sólo una pequeña cantidad de eventos.
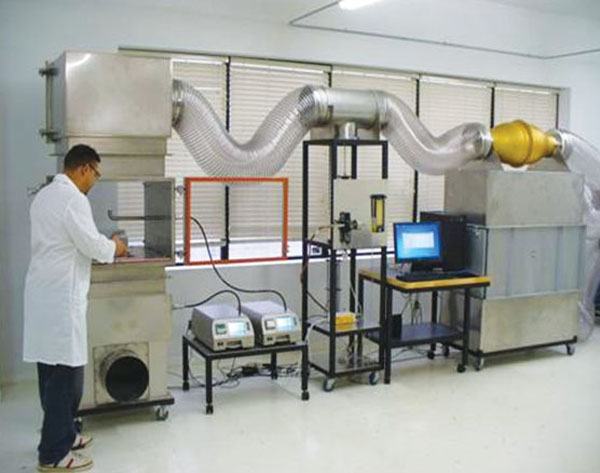
EN 1822-3:2009. Como tercer parte, en la malla plana se mide la eficiencia del tamaño de las partículas y se determina el tamaño de partícula más penetrante (MPPS, por sus siglas en inglés). Durante esta prueba, la eficiencia del tamaño de las partículas es determinada en la malla filtrante usando el conteo de partículas.
Las muestras de la malla filtrante son ajustadas en un soporte y son sometidas a un flujo de aire correspondiente con la velocidad media de filtración ya prescrita. El aerosol de prueba que proviene desde un generador es regulado; por mencionar un ejemplo está la vaporización de un solvente. Posteriormente es neutralizado y mezclado de manera homogénea con aire filtrado y guiado hacia el filtro.
Para determinar la eficiencia, flujos parciales de aerosol son muestreados por medio de una corriente ascendente y una corriente descendente en la malla filtrante. Usando un instrumento de conteo de partículas, la concentración de partículas contenidas es determinada por sus diferentes tamaños.
Los resultados de estas mediciones se emplean para realizar una gráfica de penetración contra el tamaño de la partícula para el cual la penetración es máxima. En este sentido, el tamaño de la partícula es conocido como tamaño de partícula más penetrante (MPPS).
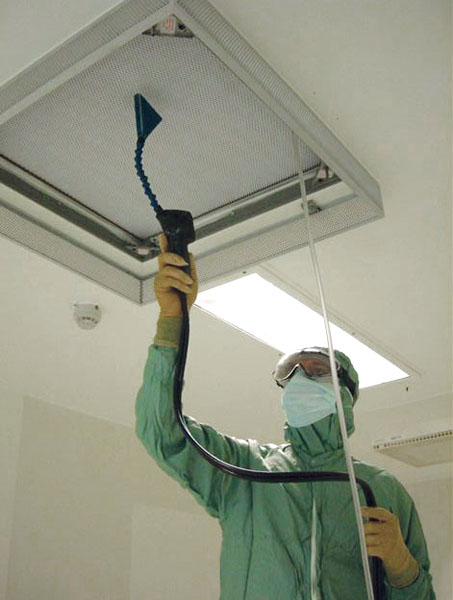
Método de prueba filtro de aire
Este método sirve para comprobar la alta eficiencia de los filtros de partículas. Dependiendo de cada parámetro, existen ciertas diferencias cuando se somete a las pruebas.
EN 1822-4:2009. La cuarta parte consiste en aplicar con un aerosol de prueba, cuyos tamaños de partícula promedio corresponden con el MPPS, una revisión a la malla filtrante para detectar fugas; la eficiencia global se calcula con las eficiencias filtradas medidas de manera individual.
La prueba de fugas sirve para realizar una prueba a la malla filtrante, de modo que se detecten aquellos valores de penetración individuales que exceden los valores permisibles.
Ahora bien, para la prueba de fugas, el filtro de prueba es instalado en el soporte y es sujeto a un flujo de aire correspondiente con la velocidad del flujo de aire nominal; más tarde, el filtro se purga y el aerosol de prueba es producido por un generador que lo mezcla con aire de prueba en un ducto de mezclado para que logre difundirse de manera más homogénea a través de la sección transversal del ducto.
La velocidad de flujo de las partículas en el lado de la corriente descendente del filtro es menor a la velocidad de flujo que llega al lado de la corriente ascendente, debido al factor de penetración media.
Las irregularidades de fabricación en el material del filtro o las fugas conllevan a la variación en la velocidad del flujo de las partículas sobre el área de la cara del filtro. También, las fugas en las áreas límite y dentro de los componentes del filtro, como el sellador, el marco del filtro y el sello del soporte del filtro, pueden tender ocasionalmente a un incremento en la velocidad del flujo de las partículas en el lado de la corriente descendente del filtro.
Para la prueba de fugas, la distribución de partículas en el flujo es determinada en el lado de la corriente descendente del filtro para detectar en qué sección los valores límite son excedidos. Las coordenadas de estas secciones son registradas.
Cuando el filtro está libre de fugas y cumple con un criterio de eficiencia global, se genera un reporte de pruebas. Es importante mencionar que un reporte de pruebas contiene un número de prueba, datos con respecto al filtro y los datos reales de la muestra; además, el estado libre de fugas del filtro es confirmado y se le asigna un número al filtro.
![shutterstock_110570789 [Converted]](http://www.mundohvacr.com/wp-content/uploads/2015/01/A0MH0076905.jpg)
Reparación de puntos de fuga
Si durante las pruebas se excede el valor específico, significa que el valor límite de penetración puede estar excedido en esta sección; en dicho caso, es necesario revisar la penetración individual. Para ello, se coloca la sonda en las coordenadas en las que el valor fue detectado en la prueba de escaneo, con el objetivo de encontrar el punto con el máximo índice del conteo.
El índice de conteo es medido en ese punto con una sonda estacionaria, donde la concentración de aerosol en el lado de la corriente ascendente es también medida de forma continua o intermitente. Un filtro puede ser reparado de ser necesario y será sujeto de nuevo a las pruebas descritas anteriormente.
Es importante resaltar que todas las reparaciones en conjunto (incluyendo aquellas realizadas por el fabricante) no obstruirán o restringirán más de 0.5 % del área de la cara del filtro; esto, sin incluir el marco. Asimismo, la longitud máxima de cada reparación individual no excederá más de 3 centímetros, mientras que el criterio para las reparaciones alternas será acordado entre el comprador y el vendedor.
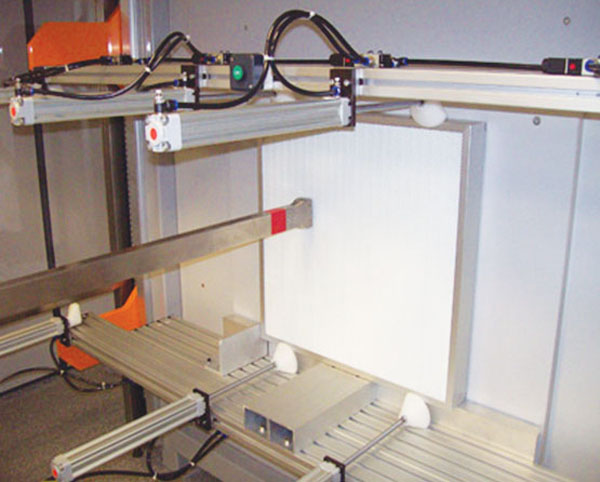
Prueba de hilo tratado
Dentro del marco de trabajo de las diferentes pruebas, la prueba de hilo tratado puede usarse para buscar fugas en las clases de filtro E 12 hasta H 14, en lugar de usar la prueba de escaneo. La prueba de hilo tratado también es aceptable como un procedimiento de prueba de referencia para los filtros que no pueden ser sujetos a una prueba de escaneo debido a su forma de elaboración.
En la prueba de hilo tratado, la ausencia de fugas se demuestra de manera visual, pues el filtro es colocado de manera horizontal en un difusor o en una caja de filtración, y es sujeto a un aerosol en gota a base de petróleo.
EN 1822-5:2009. La quinta parte de este estándar tiene que ver con la prueba de eficiencia de las mallas filtrantes que no pudieron ser sujetas a las pruebas, de acuerdo con la parte cuatro, debido a su diseño. El muestreo de la corriente descendente para determinar la eficiencia global se realiza utilizando una sonda de muestreo estacionaria.
———————————————————————————————————————————————-
Édgar Uribe Arciniega
Ingeniero Químico egresado de la Universidad Tecnológica de México. Ha tomado diversos cursos sobre distribución de aire en hospitales y hoteles, en aplicación de sistemas de aire-agua, proyección de edificios sustentables y LEED. Actualmente, estudia una Maestría en Administración de Negocios y un diplomado en Finanzas. Es ingeniero de Ventas para TROX México.