El desarrollo de procesos mediante automatismos ayuda a una empresa a ejecutar con mayor eficacia sus actividades. Sobre todo en el sector industrial, donde los volúmenes de materiales y demandas son mayores, contar con sistemas automatizados representa una ventaja competitiva
Redacción
Los retos que enfrentan las industrias de procesos se han multiplicado por la inestabilidad de la economía mundial, panorama en el que las demandas del sistema de control de procesos aumentan, haciendo de ellas más que simples funciones de regulación.
El sistema de control se convierte, por tanto, en una herramienta para manejar la planta, recortar el consumo de energía, reducir costos, disminuir las emisiones y proporcionar información rápida y precisa del piso de campo para apoyar la producción y las decisiones de negocios. Todo ello puede traducirse en una mejor administración de las plantas y una garantía para la seguridad del personal, de la planta y del medioambiente, además de que perfecciona el uso de activos, mejora la rentabilidad de la planta y optimiza los costos mientras se mantiene el nivel de calidad adecuado.
Para los equipos de ingeniería, ayuda en la implementación de estándares, en la reducción de tiempos al momento de ejecutar los proyectos, gestiona los equipos de ingeniería local y remota y en la administración del sistema desde una ubicación única.
En el caso de los operadores, se podrá asegurar la estabilidad del proceso, anticipar las fallas, priorizar acciones, actuar en alertas importantes de manera más inmediata, implementar programas de mantenimiento más efectivos y estandarizar los procesos de mantenimiento.
Para enfrentar dichos retos se requiere de un sistema de control que no sólo sea fácil de diseñar y mantener, sino que presente una imagen clara de lo que está sucediendo en su proceso. Se necesita un sistema de control que pueda integrarse fácilmente con dispositivos de terceros y que aporte un valor agregado, como la función del historiador, y la funcionalidad que brinda el Sistema de Ejecución de Manufactura.
En resumen, se necesita de un sistema que impulse el aumento del retorno en los activos y cumpla con las necesidades de su aplicación. Las características únicas, como el acceso a datos globales, la alta disponibilidad y las arquitecturas distribuidas, aunado a la redundancia Hot Standby, a fin de cumplir con los requisitos para automatizar procesos.
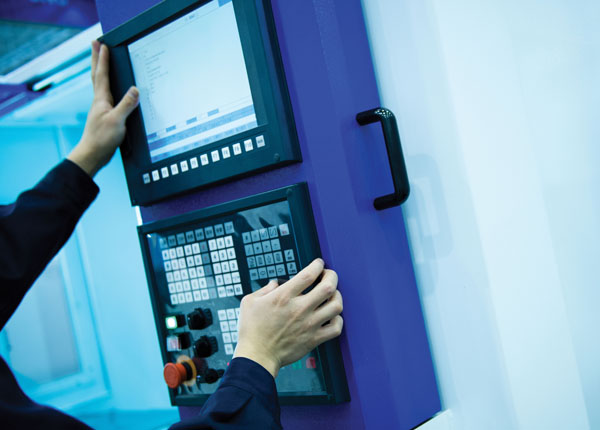
Qué se requiere
Gestión de energía y un Centro de Control de Motores de Energía Inteligente (iPMCC, por sus siglas en inglés), que optimicen el consumo de energía; medidores inteligentes, un adecuado manejo de velocidades variables que hagan más eficiente el uso de energía y, sobre todo, un software de gestión de energía que mida y analice.
Dentro del sistema de ejecución de manufactura será imprescindible tener acceso en tiempo real a la planta y a la información comercial, lo que permitirá que personal clave logre identificar y actuar en oportunidades para impactar, simultáneamente, en la cadena de suministro, se cumplan las regulaciones, se maximice la eficiencia del proceso y se asegure la producción.
También es necesario un sistema de redes en el que la comunicación sea transparente entre todos los componentes del sistema y en el que la tecnología de Ethernet sea estandarizada según los protocolos industriales. Igualmente, tendrá que servir como apoyo a los sistemas de redes y dispositivos dedicados que incluyen Modbus TCP y Ethernet / IP.
Por otro lado, el sistema de redes deberá ser un soporte para los buses de instrumentación dedicada, como son el Profibus PA, el Fieldbus Foundation y el HART.
En términos de operación, habrá que establecer un vínculo entre el operario y el proceso que sea de fácil navegación, con una gestión de alarmas efectiva y con una tendencia avanzada en la visualización de procesos; también ofrecer un rango de opciones para el cliente, sean clientes web, Asistentes Digitales Personales (PDA, por sus siglas en inglés) o que monitoreen desde teléfonos inteligentes.
Una característica más tendrá que ver con el control, pues serán necesarios controles de proceso programables que cumplan con los requisitos de seguridad. Es mejor contar con procesadores intercambiables en marcha, módulos de entrada / salida y fuentes de alimentación, lo que hará al sistema más funcional.
En cuanto al historiador, éste es un elemento indispensable, debido a que se encargará de recopilar los datos de proceso, calidad, energía y otros, de toda la planta o de sus divisiones, por lo que tendrá que generar informes detallados que ayuden en el proceso de toma de decisiones para que posteriormente se estandaricen los procesos de mejor forma y sean más seguros los sitios de trabajo.
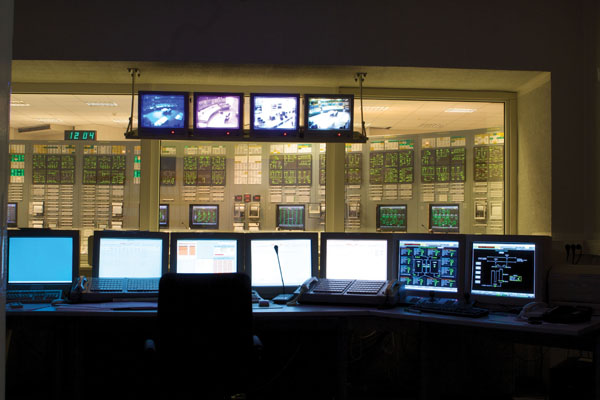
Manejo
El entorno de manejo del sistema deberá ofrecer a los operarios los datos que necesitan, junto con la personalización de las funciones que requieren para manejar el proceso como más les convenga.
Unificar los sistemas de control de cada sitio local y de acuerdo con el propio proceso permitirá un mayor control en la planta, por lo que será necesario tener una lista de alarmas unificadas y la capacidad de comparar datos con tendencias a través de múltiples áreas, todo desde un agrupamiento centralizado.
Igualmente, se debe buscar extender los manejos de la planta desde el cuarto de control hasta el piso de la planta, por lo que es importante tener Interfaz Hombre Máquina dedicados a éste y que se integren con el propósito de resistir los rigores de tales entornos.
La clave para impulsar la eficiencia en el manejo de la planta es poder ofrecer a los operarios una información clara sobre el proceso. Por ello, el sistema no sólo deberá proporcionar funciones avanzadas de alarmas y análisis de tendencias, también tendrán que estar diseñados para apoyar tanto los datos marcados por el tiempo, como a los datos en tiempo real en un entorno de operaciones único.
Ahora bien, para diagnosticar la causa de una problema y las circunstancias que rodearon al incidente, la función de lista de alarmas tendrá que brindar al personal de operaciones un método muy flexible para el filtrado y la clasificación de alarmas activas y de alarmas históricas, para apoyar la agrupación de filtrado, la clasificación de alarmas y el análisis jerárquico. Concerniente a ello se tiene el análisis de procesos, que integra las alarmas, y la tendencia de la información con comentarios del operario en una vista única para un incidente, dando pie a una solución rápida y a evitar sucesos de tal índole.
Comunicación
El acceso a la planta y a los datos del proceso desde fuera de la planta mediante clientes web y dispositivos móviles inteligentes, PDA, por ejemplo, o teléfonos móviles es muy común en la actualidad.
Este tipo de funcionalidad se ha diseñado para personas que tienen que acceder a la planta en tiempo real y procesar información desde lugares remotos, motivo por el cual los controladores de automatización deberán ser programables y diseñados de acuerdo con las necesidades de la industria de procesos. Es recomendable que el hardware sea modular, escalable y que admita un amplio rango de módulos de entrada y salida, junto con la conexión de dispositivos inteligentes y de instrumentación.
Asimismo, los controladores deberán admitir opciones de alta densidad para reducir el espacio de los gabinetes y el costo de los sistemas, ofrecer un recubrimiento conforme a ambientes hostiles y altos niveles de aislamiento, para inmunidad al ruido en entornos eléctricos difíciles; también la posibilidad de distribuir el sistema de I / O en el área e instalarlo cerca del proceso. Para ayudar a reducir el cableado y los costos de instalación es un punto extra.
De preferencia, cada procesador será multitarea, así que sus algoritmos de control, comunicación y el proceso de I / O tendrán que ser flexibles. En el mercado ya existen, incluso, controladores que admiten los cinco lenguajes de programación IEC 61131-3, sin restricción para proporcionar un amplio rango de opciones.
PlantStruxure es un sistema de colaboración que permite que las empresas de infraestructura e industriales cumplan tanto con las necesidades de automatización, como con los requisitos crecientes del manejo de la energía, y, en un entorno único, de la energía medida y los datos de procesos, donde sea posible analizarlos y utilizarlos con la finalidad de producir una planta optimizada de forma integral.
—————————————————————————————————————————————————–
Con información de Schneider Electric México