Los productos electrónicos suelen generar mucho calor. Una novedosa propuesta para facilitar su enfriamiento aprovecha las prestaciones de la refrigeración por agua con la facilidad de uso de la refrigeración por aire
Bruno Agostini, Daniele Torresin, Timo Koivuluoma y Yong X. Wang / Imágenes: cortesía de ABB
La densidad de pérdida de calor en la moderna electrónica de potencia puede superar los 100 W/cm2 en el chip y 30 W/cm2 en el sumidero de calor; cifras que podrían ser mayores en productos futuros.
A pesar de que el agua es un medio muy eficaz para la refrigeración de electrónica de potencia, no suele ser ni deseable ni práctica. Sucede lo contrario con la refrigeración de dos fases, ya que utiliza fluidos dieléctricos en configuraciones pasivas y logra coeficientes de transferencia de calor muy altos.
Algunos de los equipos que se utilizan para satisfacer las necesidades de refrigeración de dos fases son los intercambiadores de calor por termosifón, de los cuales existen el compacto de dos fases y el de aire-aire para refrigeración de espacios cerrados.
El diseño de ambos equipos está basado en tecnología automovilística que emplea numerosos tubos multipuerto extruidos con canales capilares dispuestos en paralelo y soldados a una placa base, diseñada para soportar los módulos de electrónica de potencia. Además, muestran las prestaciones de la refrigeración por agua con la facilidad de uso de la refrigeración por aire.
Llevar a un completo desarrollo esta tecnología de refrigeración exigió un trabajo detenido de facilidad de fabricación, fluidos utilizables, seguridad, normativa aplicable y una investigación a fondo de los requisitos de rendimiento, seguridad y fiabilidad.
Principio de funcionamiento
Esta tecnología trata de sustituir los actuales sumideros de calor de aluminio refrigerados por aire con un enfriador por termosifón compacto y de altas prestaciones, basado en un intercambiador de calor de automóvil.
Las ventajas se encuentran en un tamaño total reducido, mayor densidad de potencia, menor ruido del ventilador y mejor diseño mecánico.
El enfriador está hecho de tubos extraídos multipuerto (MPE) paralelos de aluminio cuyos extremos se conectan a un tubo colector en las partes superior e inferior. El enfriador se divide en un evaporador con una sección ascendente en la parte inferior y un condensador con una unidad descendente en la superior. El tubo MPE se forma por varios minicanales (normalmente entre 7 y 13) en paralelo. Algunos de ellos están dedicados a la evaporación y, por tanto, van soldados a una placa base, donde se fija la electrónica productora de calor; el resto de los canales lleva aletas refrigeradas por aire para la condensación. Cada uno de los tubos MPE se comporta como un termosifón individual. Una ventaja de estos sistemas es la posibilidad de seleccionar el número y la longitud de los tubos MPE para satisfacer los requisitos de refrigeración.
Fabricación y prestaciones
La buena resistencia a la corrosión, la conformabilidad y la elevada conductividad térmica hacen del aluminio un material ideal para la construcción del sistema de refrigeración. En la fabricación se utiliza soldadura de aluminio Nocolok, que es el método preferido para producir intercambiadores de calor para automóviles, tales como radiadores, condensadores, evaporadores y núcleos de calentador.
En cuanto a las prestaciones, se han comparado las de la refrigeración por sumidero de calor y por agua. El rendimiento del enfriador de dos fases se encuentra entre el del sumidero de calor clásico y el del enfriador por agua, con una resistencia térmica 50 por ciento menor, apróximadamente. Además, la pérdida de presión del aire es normalmente seis veces menor que la del sumidero de calor.
Fluidos utilizables
Los refrigerantes de interés para el sistema en el grupo de hidrofluorocarbonos (HFC) son el R-134a y el R-245fa. Estos HFC son muy estables térmicamente y tienen buena compatibilidad con casi todos los materiales. Sus propiedades termodinámicas y de transporte varían entre bastante buenas y muy buenas, y permiten una elevada eficiencia de refrigeración. Se utilizan masivamente desde los años 1990 en muchas aplicaciones.
Los HFC no contienen cloro y, por tanto, no dañan la capa de ozono. Pero, por su larga vida en la atmósfera, ejercen un fuerte efecto invernadero con un elevado Potencial de Calentamiento Global (PCG). La nueva legislación sobre control de uso y emisiones de HFC prohibirá el R-134a y el R-245fa, después de 2025. Serán sustituidos por los R-1234ze o R-450A y R-1233zd, que tienen un PCG mucho menor y ofrecen las mismas prestaciones.
Por lo que se refiere a la seguridad del fluido, las pequeñas dimensiones de los termosifones de tubos MPE hacen que no se vean afectados por vasijas de presión o elementos de regulación relacionados. Así pues, las normas internacionales sobre PCG afectan muy poco a los dispositivos de dos fases, pues son herméticos y están clasificados como equipos de refrigeración estacionarios.
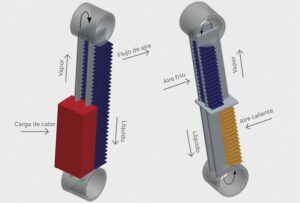
Tensión de rotura
Cuando un aparato se utiliza en un entorno de alta tensión, la tensión de rotura adquiere mucha importancia. La correspondiente al R-134a es superior a la del aire, siempre que el valor de la presión multiplicado por el entrehierro no supere 1 bar mm. Si hay fugas de refrigerante a presión atmosférica, el aislamiento eléctrico excederá al del aire puro hasta 5 kV, para cualquier distancia no mayor de 1 mm.
Pasado este punto, la capacidad de aislamiento estará entre la del R-134a y la del aire. La conclusión es que, para aplicaciones de baja tensión, el aislamiento mejora, mientras que, para alta tensión, podría necesitar una mayor separación en comparación con el aire puro. Las conclusiones son idénticas para el R-245fa.
Herramienta de diseño
Se empleó un modelo de flujo de dos fases, numérico y unidimensional, como representación idealizada del termosifón. El modelo utiliza la solución de las tres ecuaciones de conservación (masa, momento y energía) combinada con un algoritmo de minimización para determinar el caudal másico, la temperatura de saturación y la calidad de vapor que sale del evaporador dentro del circuito.
Se han utilizado correlaciones para caracterizar el flujo de dos fases. Se ha acoplado un solucionador de distribución del calor en 3D al solucionador del termosifón, para predecir la temperatura de la unión de silicona, así como para tener en cuenta la envoltura del módulo y el efecto del coeficiente de transferencia de calor de ebullición sobre el flujo de calor local, que afecta a la distribución.
Una tecnología probada
El sistema de refrigeración autónomo es una tecnología consolidada lista para su integración en convertidores de potencia y apta para proporcionar las prestaciones de la refrigeración por agua con la facilidad de uso de la refrigeración por aire.
Los métodos y componentes de fabricación relacionados con este tipo de sistema son de la tecnología más reciente. Su historia de fiabilidad se debe a decenios de experiencia en la industria automovilista; además de que la tecnología ha sido probada a fondo en los laboratorios y sobre el terreno.
Bruno Agostini y Daniele Torresin
ABB Corporate Research (Dättwil, Suiza)
Timo Koivuluoma
ABB Oy (Helsinki, Finlandia)
Yong X. Wang
ABB AG (Brilon, Alemania)