La última tendencia de fabricación discrecional se conoce como lot size one. La rentabilidad de estos sistemas de producción depende de su autoconfiguración y adaptación a cualquier diseño de producto individual, sin intervención humana y con una calidad perfecta
Fotografía de portada: Imagen 1. Sensor KNX ABB-tacteo
Dirk Schulz y Lars Simora / Imágenes: cortesía de ABB
La personalización masiva se sitúa a la vanguardia de la fabricación discrecional, ya sea en el sector de la automoción o de los productos básicos. Uno de los motores de Industria 4.0 (la tendencia actual de la automatización y el intercambio de datos en tecnologías de producción) es la fabricación rentable de bienes de consumo altamente personalizados en lotes pequeños, literalmente de un sólo ejemplar (lot size one).
Un buen ejemplo de producto ideal para la era lot size one es el elemento de control KNX ABB-tacteo® para edificios inteligentes. Éste permite diseñar la funcionalidad y la estética de cada producto individual; sin embargo, plantea dos problemas:
- El sistema de producción debe autoconfigurarse para cualquier diseño individual sin necesidad de intervención humana, para ser rentable
- La calidad de cada producto individual debe ser perfecta, ya que prácticamente no se producen repuestos
Al diseñar la línea de producción se hizo patente que los conceptos de integración establecidos no proporcionarían flexibilidad ni control de calidad necesarios. La consecución de estos objetivos se materializó, utilizando conceptos de Industria 4.0, como el gemelo digital y los protocolos M2M (máquina a máquina), como OPC UA.
Fabricado previo pedido
El sensor KNX ABB-tacteo es un elemento de control capacitivo para la automatización inteligente en hoteles, oficinas y edificios públicos y residenciales. Cumple las exigencias del diseño moderno, los niveles más altos de calidad y, sobre todo, de comodidad para los residentes, de tal forma que resulta fácil controlar desde persianas, alumbrado, climatización y calefacción, hasta la reproducción de medios y el acceso a las habitaciones.
El número de funciones que proporciona es variable y viene determinado por las necesidades y los deseos del cliente, gracias a un configurador en línea. Esto significa que el consumidor tiene el control directo sobre el diseño del producto final, al tiempo que se mantienen las ventajas de la red de valor tradicional (imagen 2), en la que los mayoristas se ocupan de la distribución e instaladores expertos integran los productos de automatización de edificios, atendiendo a las necesidades de los clientes.
El elemento de control es de cristal de alta calidad con los iconos diseñados sobre un recubrimiento de fondo opaco, tras el cual se encuentra la electrónica del sensor KNX. Las fases de fabricación son las siguientes: después de colocar los paneles sobre una bandeja, un láser de infrarrojo cercano (NIR) elimina el recubrimiento acorde a la forma de los iconos diseñados.
A continuación, una impresora digital vuelve a cubrir las zonas transparentes para proporcionarles el nivel de transparencia necesario para cada icono. Una vez seca la tinta, se monta la electrónica y el producto terminado se prueba antes de enviarlo al mayorista. Todas las características físicas, electromecánicas y de software del producto se individualizan, según el diseño del cliente.
Calidad perfecta en cada fase
El contexto de Industria 4.0 admite numerosas innovaciones, como las máquinas autónomas que negocian entre sí el calendario de producción, o los productos inteligentes que se conducen de forma autónoma a lo largo de la producción.
El primer problema es decidir qué conceptos son útiles para un entorno de producción en particular. Teniendo en cuenta la libertad de diseño con la que cuenta el consumidor, cada elemento de control es un producto único. La calidad se convierte en una prioridad máxima, pues de lo contrario habrá que fabricar de nuevo y eso retrasa el pedido.
Hoy en día, la falta de digitalización es determinante para los problemas de calidad: el material se obtiene y se transporta de forma manual, atendiendo a los datos del pedido que figuran en un papel. Aunque los datos de diseño están disponibles en formato digital, se transmiten a las máquinas de forma manual en medios extraíbles. Los datos importantes para la calidad, como los valores de calibración de las máquinas, no se guardan ni se pueden auditar, si la inspección de calidad del producto terminado revela algún defecto.
En la producción individualizada es vital detectar los fallos lo antes posible y, preferiblemente, evitarlos por completo. Este tipo de producción debe ser muy adaptable, resiliente, y tanto los operadores humanos como las máquinas deben colaborar para cerrar el ciclo de la calidad.
Digitalización completa con gemelos digitales
La producción individualizada se apoya en dos puntos clave:
- La transformación de materiales adaptables dentro de las máquinas
- La interoperabilidad digital entre ellas
Aunque hay tecnologías de materiales como los láseres NIR o las impresoras digitales, las máquinas aún tienen que aprender a trabajar juntas de forma natural para conseguir la eficiencia y calidad necesarias. En la actualidad, las máquinas se conectan por cable o con software PLC. Esta disposición ofrece una integración estrecha, pero supone un esfuerzo considerable y no ofrece mucha flexibilidad para nuevas variantes de productos, excepto las diseñadas desde el inicio.
Conseguir una producción adaptable requiere integración basada en una conexión más abierta, para que la reconfiguración de la línea sea flexible con el mínimo esfuerzo. Esto se consigue con gemelos digitales que presenten las habilidades específicas de cada máquina en un formato común en la red, con independencia de cualquier conexión cableada o programada.
Para evitar cambios de medios, el diseño del producto junto con los datos de calidad y pedidos se representan de la misma manera. Así, organizando los gemelos digitales de la máquina según el diseño del producto, cualquier reconfiguración del programa se traslada sin cambios a las fases de producción en el mundo físico y la información sobre calidad se refleja en el dominio de éste.
Usando el concepto de gemelo digital, el elemento de control KNX ABB-tacteo pasa por cada estación de producción. Cuando llega, el cristal se escanea para obtener la aprobación, los datos de diseño y los parámetros de proceso para la siguiente fase de producción. Para ello, la máquina contacta con el servicio de planificación del sistema ABB Ability™ Operations Data Management Zenon, que replica automáticamente la receta del producto a partir del sistema de ERP y almacena el historial de producción del cristal individual.
Una vez procesado, se informa al servicio de planificación junto con los datos de seguimiento de la calidad. El cristal pasa a la siguiente estación siguiendo las indicaciones de gestión de operaciones y como se muestra en la HMI (interfaz hombre-máquina) para dirigir al trabajador. En los pasos normales de trabajo, los operadores de la estación interactúan con la máquina utilizando un panel de automatización. Las fases manuales, como el transporte de materiales, se guían y se supervisan de forma electrónica.
Para garantizar la interacción correcta entre las máquinas, los servicios y los operadores humanos, las máquinas y sus gemelos digitales se extraen de una plantilla de diseño común (imagen 3). También resulta más fácil añadir o reemplazar máquinas que siguen este patrón, porque se conectan de forma natural al sistema de producción existente.
El elemento de control KNX ABB-tacteo es un producto inteligente: la identidad de cada cristal genera activamente su propia producción y los pasos descritos permiten cerrar el ciclo de la calidad sobre la base de su memoria global.
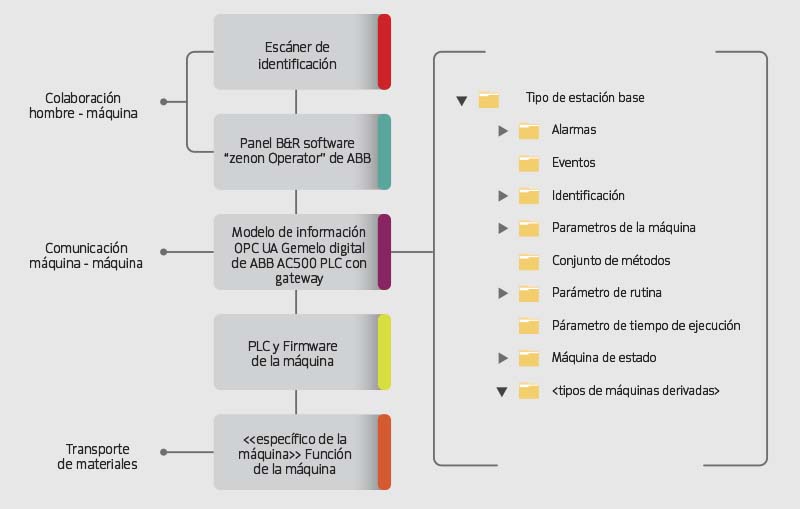
El diseño de gemelos digitales
El proceso de producción descrito depende de una combinación de datos muy diversos, unos relacionados con el diseño del producto, otros con su fabricación, otros con una máquina concreta, y otros describen información común a todos los productos o máquinas.
Para crear estos gemelos digitales, lo mejor es crear primero un modelo de información de OPC UA descendente desde la perspectiva del conjunto de las fases de producción, como se muestra en el centro de comunicación (imagen 4). El modelo no se divide hasta la etapa siguiente y se asignan componentes a los servicios de software y las máquinas correspondientes.
La mejor forma de actualizar las máquinas con este modelo es usar un PLC AC500 como pasarela de OPC UA integrada. Esto exige colaboración estrecha de los diseñadores de información, el integrador y los fabricantes de máquinas para que las máquinas reales se puedan conectar sin más en la fábrica y formar el sistema de producción deseado.
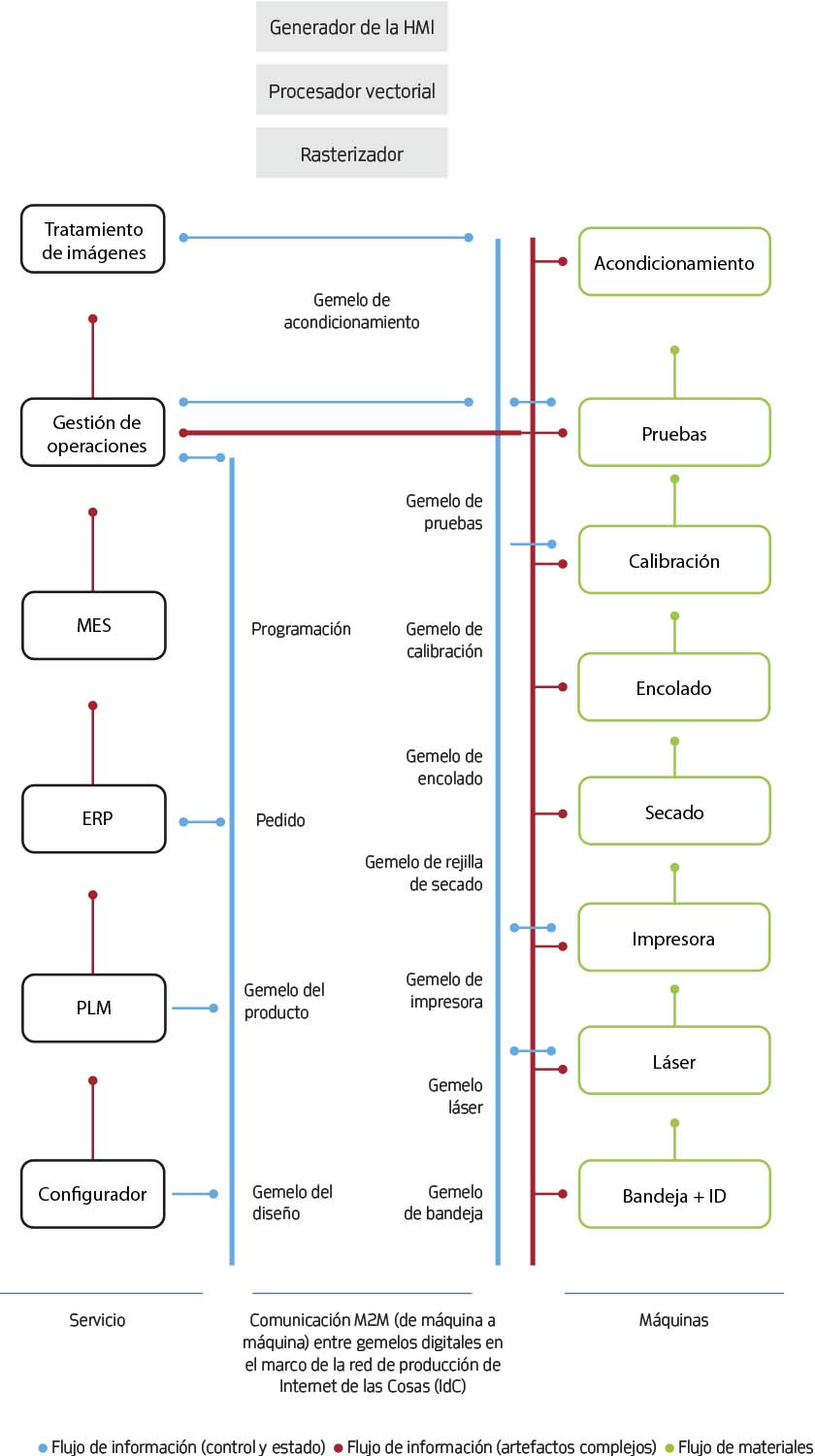
Industria 4.0 para todo
El diseño de la línea de producción de ABB-tacteo aportó información de primera mano sobre las necesidades de los fabricantes de máquinas y los diseñadores de producción en el camino hacia la Industria 4.0.
El control de calidad perfecto y la reconfiguración automatizada son los principales retos que debe abordar una solución de automatización, especialmente en el ámbito de la producción individualizada. Estos retos se pueden superar con conceptos de Industria 4.0, como los gemelos digitales, los productos inteligentes y las tecnologías M2M como OPC UA.
Aunque la producción individualizada exige hoy una importante inversión inicial, los presupuestos anuales deben cubrir las soluciones futuras para ser competitivos. Para tal fin, las máquinas especializadas deben aprender a trabajar juntas desde el principio.
De este modo, los proveedores de automatización deben suministrar procesos, herramientas y normas que permitan a los diseñadores de producción, a los fabricantes de máquinas y a los integradores crear fácilmente sus gemelos digitales de manera independiente, y después ejecutar pruebas de integración virtual incluso antes de la construcción y la puesta en servicio de las máquinas físicas.
En la actualidad, los productos prémium, como el elemento de control KNX ABB-tacteo, son magníficos catalizadores que impulsan este tipo de innovación. Pero la idea es ofrecer la plataforma Industria 4.0 no como producto prémium, sino como solución fabricada en serie que se pueda aplicar a todo tipo de producción, desde grandes fábricas hasta pymes.
—–
Dirk Schulz, ABB Corporate Research Ladenburg Alemania
Lars Simora, Busch-Jaeger Elektro Lüdenscheid Alemania
Artículo retomado de ABB Review. Colaboración autónoma 04/2018