Hoy en día, el reciclaje para la fabricación de empaques representa una opción sustentable para el sector industrial; sin embargo, para que el cartón pueda tener una nueva vida, es necesario un estricto proceso que incluye factores como el control de la temperatura y la humedad, algo que sólo es posible gracias a los sistemas de climatización
Ámbar Herrera / Fotografías: cortesía de Smurfit Kappa
Fotografía superior. Los rollos de papel liso son la materia prima para la fabricación de cajas de cartón plegadizo y corrugado
A menudo no se repara en las cosas más simples, como la utilidad de una buena y resistente caja de cartón, hasta que se realiza una mudanza y los brazos no alcanzan para cargar con todos los objetos; entonces, se hace patente la importancia de lo que parecen unos simples trozos de papel. Los empaques forman parte de la vida diaria y son más complejos de lo que se piensa; después de todo, su uso es tan variado que pueden llegar a contener enormes piezas de ensamblaje industrial o enfrentarse a condiciones extremas de temperatura y humedad, como las de la cadena de frío.
Tan sólo en 2019, la Asociación para las Tecnologías de Envasado y Procesamiento (PMMI, por sus siglas en inglés) proyecta un crecimiento de entre el 4 y 4.5 por ciento para la industria del empaque y el envasado en México, misma que representa el 1.8 por ciento del producto interno bruto nacional.
Los materiales más usados para el embalaje son el plástico y el cartón; sin embargo, en los últimos años, el factor ambiental ha jugado más a favor del segundo y, en particular, del corrugado, pues el 80 por ciento de su fabricación se realiza con material reciclado. El crecimiento anual en la demanda de corrugado oscila entre el 3.5 y 4 por ciento a nivel mundial, impulsado por el comercio electrónico, la impresión digital y la sostenibilidad, señala el informe The Future of Corrugated Packaging to 2023, elaborado por Smithers Pira, la autoridad mundial en las cadenas de suministro de la industria de embalaje, papel e impresión.
Pero, para que el cartón pueda tener una nueva vida, se requiere de un proceso con estricto control de diversos factores ambientales, el cual no sería posible sin el respaldo de los sistemas de climatización. Para entender mejor esta cuestión, Mundo HVAC&R entrevistó a los expertos de Smurfit Kappa, empresa dedicada al embalaje de corrugados que cuenta con más de 50 años de presencia en México.
“La estabilidad del cartón se alcanza con una temperatura de 23 °C y un 50 % de humedad relativa”: Luis Mercader, gerente general de la planta de Reimpresión de SMURFIT KAPPA
Desde la fibra a la caja
El Complejo Cerro Gordo, ubicado en Ecatepec de Morelos, es la planta principal de la compañía europea, la cual cuenta con más de 3 mil 700 trabajadores en el país. En entrevista, Erick Casareal, gerente de Seguridad y Salud Ocupacional, comenta que el lugar alberga a la división de reciclado, la parte de fibras y molinos, el sitio de plegadizos (donde se hacen las cajas de cartoncillo), el de corrugados (donde se fabrican las cajas de cartón) y el área de ventas.
“En México, todo es a base de papel reciclado. Se inicia en el área de fibras, con el papel que se recolecta de diferentes centros como Walmart, Chedraui y Costco, después, pasa a los molinos en donde el material se licúa, mezcla y procesa para hacer cartón nuevo”, explica Casareal (Figura 1).
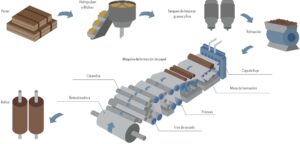
Por otra parte, Luis Mercader, gerente general de la planta de Reimpresión y de las plantas de Plegadizos de Naucalpan y Cerro Gordo, señala que la temperatura y la humedad son factores indispensables para que los empaques sean óptimos. “La estabilidad del cartón se alcanza con una temperatura de 23 °C y un 50 por ciento de humedad relativa”.
El proceso de fabricación, explican los entrevistados, comienza en los molinos, allí se desfibran y muelen con agua alrededor de 1 mil 200 toneladas de cartón por día para formar una pasta que se refina en varios procesos hasta quedar libre de impurezas (Figura 2). Ésta pasa por una serie de rodillos giratorios o prensas para extraerle la máxima cantidad de agua (hasta un 50 por ciento). Posteriormente, la pasta se envía a una mesa de formación para fabricar una hoja de papel que puede llegar a pesar de 120 a 330 gramos por metro cuadrado. Como siguiente paso, atraviesa el tren de secado, formado por cilindros huecos rotatorios en donde se le inyecta vapor para bajar su nivel de humedad. “En un inicio, la hoja se forma con un 99 por ciento de agua y solamente el uno de fibra, pero al final queda con un siete por ciento de agua”, dice Mercader. Una vez terminada, se enrolla a una temperatura de 40 °C y se rebobina durante 15 minutos para que entre en temperatura ambiente.
Tecnología HVACR
Durante el secado del papel, la temperatura se debe elevar por encima de los 100 °C y alcanzar una humedad del 7 u 8 por ciento. Para controlar estos valores se requiere del uso de sensores y termómetros específicos. También se utilizan escáneres de radiación que cada 40 segundos hacen un barrido a lo ancho de la hoja para medir su calibre, humedad, peso y demás aspectos, con el fin de “maximizar la actuación y desempeño de la producción y el empaque final”, indica Luis Mercader.
Asimismo, la ventilación en las áreas de trabajo es indispensable para garantizar que las operaciones sean exitosas. En el área de los molinos, por ejemplo, se emite mucha agua a la atmósfera y la humedad podría perjudicar a los equipos; por ello, esta zona cuenta con una gran campana de extracción para mantener el ambiente controlado. De igual modo, tanto los tableros electrónicos de las máquinas como los equipos de instrumentación y control incorporan sistemas de refrigeración para evitar el sobrecalentamiento.
En la planta también se usan bombas centrífugas para controlar y bombear el agua hacia el hidropulper o molino, que es donde se mezcla todo el material reciclado, comenta el gerente general de la planta.
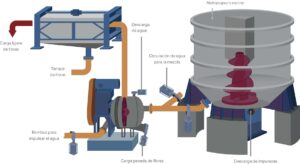
Seguridad, automatización y eficiencia
Erick Casareal señala que otro factor muy importante para la producción es la seguridad. En consecuencia, la planta cuenta con un sistema contra incendios compuesto por hidratantes, monitores, detectores de humo, rociadores y una cisterna de más de un millón de litros. Además, agrega que todo está interconectado a un sistema de alarmas que se activa en caso de emergencia.
En el Complejo de Cerro Gordo, todas las áreas están automatizadas para el control de los instrumentos, paneles e interruptores. Esto, al tiempo que brinda una mayor seguridad, ayuda a incrementar la eficiencia energética y el ahorro de agua.
Luis Mercader menciona que la planta recibe un alto voltaje (200 mil voltios), por lo que, para aumentar la eficiencia, tienen un sistema interno de subestaciones y están cambiando toda su iluminación a lámparas led. En tanto, también el vapor que se genera en la planta se recupera mediante un tanque de flasheo para usarlo de nuevo en las calderas en un ciclo continuo.
La compañía, además, tiene metas fijas para la reducción en cuanto al consumo de agua y de emisiones a la atmósfera, así como para el control de los desechos, a fin de mejorar sus operaciones y ser más amigable con el medioambiente.
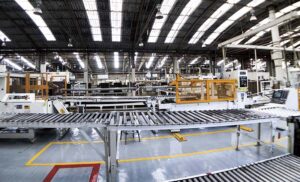
Calidad y precisión en cada proceso
El objetivo de tener un control preciso en las fases de fabricación es conseguir rollos de papel óptimos para producir los empaques de cartón corrugado y plegadizo que solicitan los diferentes clientes. Los expertos destacan que cada rollo producido pasa por laboratorios en donde se le realizan pruebas de peso, calibre, humedad, compresión, etcétera. Esto es necesario para comprobar las propiedades de resistencia del papel y ver qué tanto será capaz de soportar la estiba del cartón que se fabrique. Enfatizan que garantizar la calidad de la mercancía es muy importante, porque cuando un rollo no cumple con los estándares, se tiene que rehacer.
Cabe señalar que no todos los empaques son iguales, ya que la blancura y longitud del papel varía dependiendo de la mezcla que se realice. En el caso de los empaques elaborados para la cadena de frío, a la mezcla se adhiere un encolante especial que hace que el papel pueda soportar mejor la humedad. A estos productos se les realiza la llamada prueba de Cobb, que sirve para verificar que el cartón cuente con la cantidad de recubrimiento necesario para resistir las condiciones extremas a las que será sometido en los transportes refrigerados y durante el resto de las fases de la cadena de frío. Otra prueba es la de inmersión, que puede predecir cuánto tiempo soportará determinado empaque en un refrigerador.
Por último, Casareal menciona que, cuando la producción pasa por las pruebas correspondientes, se emite un certificado de calidad para enviarla a los clientes. La fabricación de empaques implica un largo y complejo recorrido, pero es gracias al conocimiento que hay detrás de la tecnología HVACR que se puede lograr el éxito en procesos de este tipo.