La medición correcta del aire supone beneficios tanto para los ocupantes como para los dueños de los edificios, además de proporcionar ahorros energéticos y prolongar la vida útil del inmueble. ¿Sabe cómo realizar la medición?
Una frase célebre de Lord Kelvin reza lo siguiente: “To control something, you must firts measure it”. La cita anterior significa que para poder controlar algo, primero debemos medirlo. No podemos tomar decisiones ni obtener la controlabilidad que necesitamos en nuestro sistema sin antes saber cómo se está comportando. Esta idea aplica en todos los ámbitos de la vida y mucho más en el sector HVACR, donde debemos tener ojos en nuestro sistema para poder decidir.
Otra forma de decirlo es que el control será tan bueno como la calidad de medición en el proceso. Entre más puntos de medición tengamos en el sistema, más fácil será tomar decisiones. En la actualidad, los sensores y transmisores son dispositivos que no se ven porque muchas veces están arriba, en las tuberías o en los ductos, y aunque nadie los observa son fundamentales para los sistemas HVAC.
¿Cuál es la importancia de la medición del flujo de aire? Muchos de los sistemas tienen equipos eficientes, una buena red de ductos, pero en ocasiones desconocemos si su operación cumple con los flujos y la velocidad del aire, así como la presión especificada en el proyecto.
Todos los dueños de edificios, los facility manager y la gente que se preocupa por el bienestar de su propiedad se hacen las siguientes preguntas:
1. ¿Hay suficiente aire fresco para poder ofrecer un ambiente saludable a los ocupantes?
2. ¿Puedo garantizar que mi edificio tenga aire fresco y que se esté renovando?
3. ¿Tengo la cantidad suficiente de aire nuevo para tener una calidad del aire interior (CAI)?
4. ¿Tengo el volumen de aire necesario para no desperdiciar energía y afectar la capacidad y eficiencia de mis equipos?
5. ¿Estoy seguro de que no tengo fugas de aire en los ductos?
6. ¿Mi sistema de control de presión me garantiza el volumen de aire necesario en cada zona?
7. ¿Cómo puedo incrementar la vida útil de mi edificio y simplificar su operación y mantenimiento?
Para entender esto, primero debemos comprender cómo se comporta el flujo de aire en los sistemas de aire acondicionado (AA) y entender cuáles son los estándares de medición en la industria, así como saber quién dicta las normas y especificaciones para contar con un parámetro.
El aire en sistemas HVAC
El flujo de aire es extremadamente dinámico, es decir, el aire es un fluido cuyo comportamiento es afectado por factores como la existencia de codos, ramificaciones, ductos en T, ampliaciones o reducciones de ductos. Idealmente sería preferible tener un flujo de aire laminar, pero lo más común es la turbulencia en el flujo de aire. En otras palabras, el comportamiento del flujo de aire puede cambiar dependiendo de la turbulencia existente y de la velocidad que se tenga en el ducto.
Algo muy importante que debemos considerar es que, si se requiere mantener una medición exacta, son necesarios múltiples puntos de medición, pues entre más puntos cubran toda el área del ducto, la medición será más exacta y se podrán tomar lecturas más precisas.
En la Figura 1 vemos unas mediciones en 3D donde se muestra cómo a mayor velocidad, tendremos un mayor flujo turbulento; a menores velocidades, el flujo será más estable. Esto dependerá de lo que se tenga antes de poner los sensores, por ejemplo: un codo, un ventilador, un damper, un ducto T, etcétera. Hay que tener en cuenta que en pocas instalaciones se tiene realmente el tramo de ducto recto necesario. Por ejemplo, casi siempre en los lugares donde van los ductos el espacio está limitado, por lo que normalmente tenemos varias trayectorias para llegara a la rejilla adecuada.
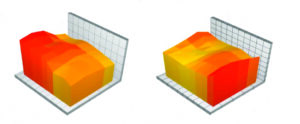
En la Figura 2 observamos un codo y el tramo de ducto recto. En este ejemplo tenemos un sensor instalado después de un tramo de 12 diámetros, después de un codo. En la gráfica, la medición es estable porque 12 diámetros es bastante aceptable. ¿Qué sucede si solamente tenemos 4 diámetros después del codo? (Figura 3). Lo que sucede es que en ciertas partes del ducto se registrará mayor flujo de aire y otras partes menos flujo, ya que el flujo del aire no será totalmente laminar cuando llegue al sensor. En ciertas partes del ducto se va a registrar mayor flujo de aire. En los codos, el aire pega en una parte del ducto y cuando comienza el ducto recto, la mayor parte del flujo de aire se pega hacia una pared y del lado opuesto al codo tendremos menos flujo.
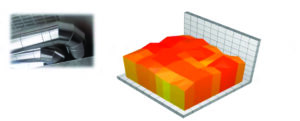
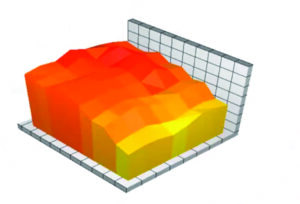
Ahora bien, si tengo sólo 0.5 diámetros después del codo, la lectura del flujo no será precisa; por tanto, no se recomienda esta acción. Pero ¿quién nos va a decir cuántos diámetros se recomiendan en la instalación de un sensor de flujo o de una estación de medición? Estas recomendaciones las dicta el fabricante de sensores, apoyado por los estándares de organizaciones como ASHRAE y AMCA, asociación que dicta las regulaciones para el movimiento.
La Figura 4 muestra un ducto con un codo recto y se observa un diámetro de 0.5 después del codo en donde se coloca el sensor. Cuando el flujo de aire pega, se genera turbulencia y la desviación de flujo es mayor a 90°, por lo que no se tendrá una buena medición. Cabe destacar que entre más tramo de ducto recto y entre más puntos de medición tengamos en el área del ducto, obtendremos una mejor exactitud en la medición.
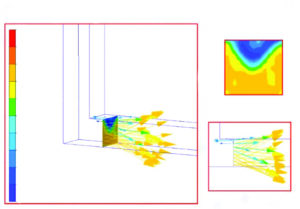
Requerimientos mínimos de instalación
Las recomendaciones sobre cuántos diámetros hay que dejar, ya sea antes o después del sensor o de la estación de medición, dependerá de cada fabricante, así como de los elementos que se tengan antes o después del sensor. La Figura 5 muestra un sensor y un ventilador centrífugo, ahí queremos medir cuánto flujo de aire se inyecta por el ducto. Para lograr la exactitud indicada en el documento técnico hay que dejar por lo menos 2x de tramo de ducto recto. Si es un ducto circular, la x se refiere al diámetro. Si es un ducto rectangular, la x se define con una ecuación: dos veces la multiplicación de la altura por el ancho del ducto dividido entre la suma del alto y del ancho del ducto. Ésta es la recomendación en casos con ventilador centrífugo.
Si se tiene un damper y quiero saber cuánto flujo se tiene después de éste, la recomendación es dejar 1/2 de x, si es que tengo algunos linealizadores de flujo y si no, serían 2x como en el caso del ventilador centrífugo. ¿Qué pasa si tenemos un codo? Después del codo tenemos que dejar 1x y si hay otro codo hay que dejar por lo menos 1/2 de x. Existen diferentes arreglos y aquí no hablaremos de todos, pero siempre es importante irse a las recomendaciones del fabricante para garantizar esas exactitudes.
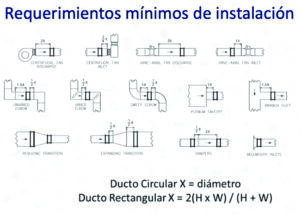
Métodos de medición
¿En qué se basan los fabricantes para asegurar que la medición sea correcta? Los fabricantes de sensores de flujo de aire se basan en el Estándar 203 de AMCA, Fundamentals Handbook de ASHRAE y en el Código de Regulaciones Federales 40 CFR 60 de Estados Unidos.
• Logarítmico lineal: El método que utiliza AMCA es el logarítmico lineal. En este método se colocan varios sensores en toda el área del ducto. En ductos redondos debe haber por lo menos ocho puntos de medición. En ductos rectangulares se deben colocar al menos 25 puntos de medición para garantizar la precisión.
• Log-Tchebycheff: ASHRAE recomienda el método Log-Tchebycheff, el cual aconseja poner 25 puntos de medición en ductos rectangulares y 18 en circulares.
• Equal área: El CFR utiliza este método de distribución, el cual especifica un mínimo de 8 a 16 puntos para mejorar el comportamiento de la velocidad.
Medición de flujo de aire en ductos
Existen diferentes tipos de instalación en las edificaciones. La más común es la medición de flujo en ductos porque proporciona un área precisa para la medición de perfiles de velocidad, es decir, se puede conocer la velocidad, el área del ducto, si hay un ventilador, damper o codo antes y después. Además, las obstrucciones más comunes en el ducto pueden ser cuantificadas, así como los requerimientos de tramos rectos.
1. Medición en la entrada del ventilador
Si no tenemos un ducto disponible, podemos recurrir a la medición en la boca o las entradas de los ventiladores. En este caso, se colocan los sensores, dependiendo del diámetro de la boca del ventilador para hacer la medición. Lo importante en este tipo de medición es que tendremos altas velocidades (arriba de 5000 fpm). En la actualidad existe la tendencia de colocar ventiladores más pequeños para obtener velocidades más altas.
2. Medición en toma de aire exterior
Con LEED v4 los edificios deben medir cuántos cfm de aire limpio toman. Ésta es de las mediciones más complicadas porque hay muchos puntos en contra. Por ejemplo, velocidades extremadamente bajas (150 FPM), ráfagas de viento direccionales o variables, rangos de temperatura entre -20 °F a 120 °F (-29 °C a 49 °C), según el lugar donde se haga la instalación, humedad variable dependiendo de la estación del año (30 a 100 por ciento), condensación, presencia de partículas que podrían tapar el sensor y normalmente no existe un tramo de ducto recto.
3. Medición en sistemas economizadores
En este tipo se ha utilizado el free cooling para aprovechar las temperaturas exteriores y así ahorrar energía en los equipos de AA. En este caso, los cálculos se basan en el control de entalpía (temperatura y humedad exterior). Es muy común en lugares con temperaturas extremas y se enfoca en el Estándar 90.1 de ASHRAE que habla sobre la eficiencia energética en los edificios. En este tipo de instalaciones los ductos tienden a ser sobredimensionados, por lo que la medición es un reto.
Dispersión térmica y presión diferencial: tecnologías de medición
Las tecnologías más utilizadas en la actualidad son la de dispersión térmica (masa) y la presión diferencial (DP). La primera se basa en el uso de dos termistores. El sensor va dentro del ducto y se pueden tener diferentes puntos de medición. El funcionamiento de los termistores consiste en que cuando uno de ellos comienza a calentarse, la velocidad del flujo de aire se determinará con ayuda de un algoritmo para saber qué tan rápido o lento se enfría en comparación con el otro termistor. Esta tecnología da muy buenos resultados, garantiza la exactitud y ayuda cuando se tiene un área muy grande de ductos, ya que se pueden poner varios sensores en línea que abarquen toda el área, aprovechando un sólo transmisor. De este modo, no es necesario que cada sensor tenga un transmisor para después mandarlos a un controlador. Luego, se podrá realizar una relación que permita hacer promedios para obtener la lectura. La tecnología de dispersión térmica se recomienda para bajas velocidades y entre sus ventajas está que no es afectada por los cambios de temperatura. Asimismo, cuando se utiliza esta solución el sensor y el transmisor siempre irán de la mano, por lo que el fabricante garantiza una exactitud como paquete, además de que cada sensor puede ser calibrado individualmente y cuenta con certificado NIST.
La tecnología de presión diferencial (DP) utiliza un tubo Pitot y es la más común. Consiste en medir dentro del ducto la presión total y la presión estática para conseguir la velocidad de presión, a través de un transmisor, para obtener el área del ducto y saber los cfm o alguna unidad en volumen de aire. Se pueden tener sensores simples o estaciones de medición, las cuales son muy prácticas y simplifican el tiempo. Cuando no se tiene el tramo de ducto recto necesario se utilizan un panal (Figura 9) que hace más lineal el flujo de aire para lograr una mejor lectura cuando llegue a los sensores.
Las ventajas de la medición de la presión diferencial son el bajo costo por punto de medición, el buen desempeño en ductos con poco tramo recto, que cumple con las normativas de AMCA, ASHRAE y CFR, además de que su exactitud de medición no es afectada por el cambio de humedad o de condensado. Su uso se recomienda para rangos de velocidad entre 400 y 18 mil fpm.
Como se podrá ver, los beneficios de la correcta medición de flujos de aire son variados. Para los ocupantes, los beneficios son mejor CAI, incremento de la productividad debido a una temperatura y humedad adecuadas y mejoras en la salud. En cuanto al cumplimiento normativo, la medición permite el cumplimiento de los estándares 62.1, 170, 90.1 y 189.1 de ASHRAE, de los códigos y normas de los edificios, la reducción del consumo energético y la simplificación de la operación y mantenimiento del edificio. Todo esto a favor del incremento de la vida útil del inmueble.