Tras la alerta epidemiológica suscitada por la influenza H1N1 en 2009, la OMS en México y el gobierno federal impulsaron un proyecto para garantizar la independencia del país en este rubro. Se construyó un laboratorio de biológicos y reactivos, encargado del resguardo de la vacuna para la influenza H1N1 y más tarde de investigar y desarrollar nuevas soluciones. Éste es el resultado
Sinaí Romo / Bruno Martínez y Vilatore Ingeniería, fotografías
La fabricación de productos biológicos en México se remonta a hace más de 100 años. Desde entonces, el desarrollo de vacunas, las actividades de diagnóstico y el tratamiento de enfermedades en la población se sirve de su contribución directa.
En la actualidad, existen en México diversos laboratorios establecidos legalmente, que desarrollan y fabrican vacunas, sueros y productos de diagnóstico. Desarrollar nuevas soluciones para atender las necesidades de los programas de vacunación del sector salud del país es una de sus actividades.
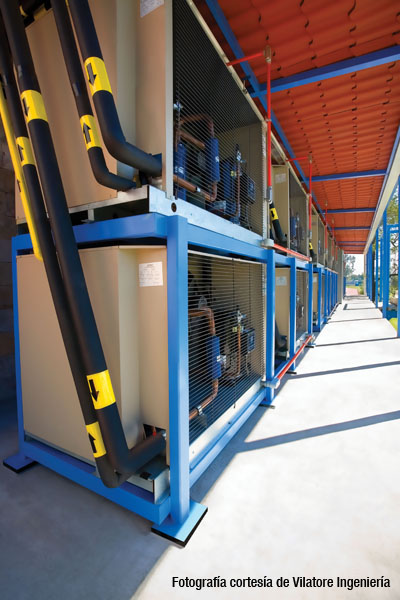
Para cumplir este objetivo, un grupo de especialistas se dedica a generar tecnologías de producción de nuevas vacunas y a mejorar las existentes. Los proyectos de investigación y desarrollo actuales se enfocan en la manufactura de vacunas virales, vacunas bacterianas, ensayos clínicos y otros biológicos.
Las plantas de producción, centros de investigación y oficinas corporativas se encuentran distribuidas en varias partes del territorio mexicano. En el caso específico de la planta productiva que resguarda la vacuna contra la Influenza, se hubo de erigir un laboratorio especial en el municipio de Cuautitlán, Estado de México.
La meta inicial del proyecto fue no depender de la producción internacional, consolidar la producción en México y lograr ahorros de divisas importantes para el país. El plan maestro pretende que, de manera gradual, se incorporen nuevos laboratorios para otros productos y vacunas que garanticen un plan epidemiológico nacional.
La epidemia nacional derivada de la influenza H1N1, o gripe tipo A, en 2009, afectó de manera considerable la salud de los habitantes y, sobre todo, provocó que instituciones de todo el mundo tomaran medidas preventivas para evitar una crisis sanitaria en el planeta. La indispensable creación de una vacuna fue la respuesta inmediata que dieron los especialistas como medida de prevención para México.
El resultado fue una instalación sanitaria con una superficie de 74 mil metros cuadrados en la que se formula, envasa y acondiciona la vacuna que evita el contagio del virus estacional.
Dada la relevancia de las actividades y del producto resguardado, el proyecto demandó una edificación ceñida a estrictos estándares de calidad constructiva y de operación. La asignación del proyecto se llevó a cabo mediante concurso; diversas empresas especializadas en ingeniería de sistemas eléctricos, HVACR y de construcción partiparon en el proceso de selección para encontrar a las más adecuadas.

El reto: seguridad y control
A Vilatore Ingeniería se le otorgó la implementación de la red fría para el centro de distribución. Con base en las exigencias del laboratorio, el equipo de la firma diseñó y puso en marcha el sistema necesario.
Las especificaciones de los equipos se basaron en normativas establecidas en un cronograma general de ejecución, en el que se detallaron los tiempos y movimientos de las diferentes etapas del proyecto. Con ello quedaron asentados los parámetros de ingeniería aplicables y el tiempo de ejecución: seis meses.
Pedro Villavicencio, director General de Vilatore Ingeniería, comenta acerca del proyecto: “La construcción de las cámaras que están instaladas en esta planta de producción significó muchos años de experiencia, tanto de ingenieros, soldadores, diseñadores, electromecánicos, técnicos y especialistas en software, pues para que se lleve a cabo un trabajo de esta magnitud es importante contar con personal calificado. Nosotros contamos con el mejor”.
El reto por superar para el desarrollo de la planta fue lograr la excelencia; consolidar un laboratorio comprometido con la innovación y la producción de vacunas y biológicos que protejan, mejoren y prolonguen la vida de la población mexicana, la razón. Se tomaron en cuenta normas internacionales para el desarrollo de especificaciones en la fabricación de cuartos fríos y fue indispensable estar certificado bajo estos paradigmas.
La labor de ingeniería que implementó la firma es de importancia vital. Una falla en el suministro de frío se traduciría, no sólo en pérdidas económicas, desencadenaría una problemática sanitaria a nivel nacional, dado que 85 por ciento de vacunas que se distribuyen y aplican a nivel nacional pasan por estas cámaras.
El ingeniero Villavicencio relata que las instalaciones se generaron para cubrir una necesidad de la Organización Mundial de la Salud en México, pues el país no contaba con una red de frío para fármacos ni biológicos. La inversión para el proyecto, así, la asumieron el gobierno federal y el propio organismo.
“Actualmente, en el sector salud la tendencia mundial es prevenir. Resulta más económico prevenir que reparar, ya que los tratamientos son más costosos. Una bacteria que en la actualidad es inofensiva en 20 años puede ser mortal. Esto se debe a que los seres vivos vamos cambiando. Por ello es tan importante crear este tipo de instalaciones, pues no solamente se trata de almacenar las vacunas, sino de crear nuevos tratamientos. Eso es lo que pretende este proyecto”, señala el ingeniero Villavicencio.
Como recomendaciones iniciales, la producción de la vacuna contra la influenza H1N1 debe contar con espacio suficiente para almacenar las unidades que se necesitan. Según parámetros mundiales, el espacio debe contar con cuartos fríos, enfriadores horizontales y enfriadores verticales para regular el frío que se proporciona.
La temperatura en el interior de las cámaras debe oscilar entre 2 y 8 grados centígrados; nunca más frío, pues la vacuna no debe congelarse. Para asegurar esto se recomienda colocarla en estantes intermedios; sin embargo, un buen sistema de control puede permitir que este objetivo se logre.
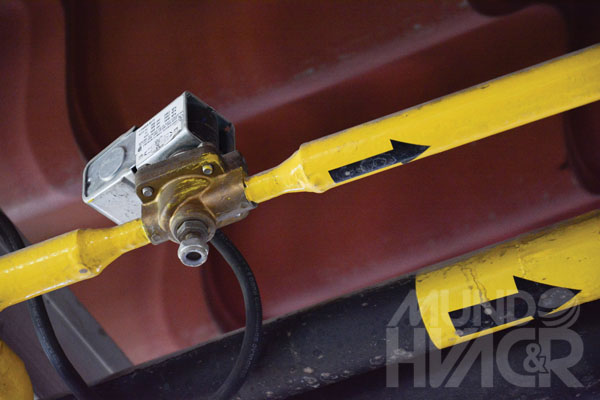
Cuarto de máquinas
Este sitio cuenta con 18 equipos distribuidos de forma independiente en el sistema. Esta característica se deriva de que cada una de las tuberías se conecta a un solo evaporador, rasgo que previene daños a otros compresores debido a la acidez que normalmente se genera en caso de que alguno fallé.
Los equipos trabajan mediante compresores tipo scroll. La elección de este tipo en específico se debe a que sufren menos desgaste que los de pistón; dado que la demanda de refrigeración es alta, han mostrado mejores resultados. Muestra de ello es que, tras cinco años de operación con los que cuenta la instalación, no se han presentado problemas de desempeño.
El cuarto tiene un tablero de control principal que le da alimentación a evaporadores y unidades condensadoras; además, cada una de ellas cuenta con un tablero individual.
Las labores de mantenimiento se realizan con regularidad; durante ellas, se verifica que las temperaturas de operación y presión sean ideales. Cabe destacar que la medición de estos rangos se realiza a diario, a fin de monitorear todo el sistema y tener certeza de su óptima condición.
Se cuenta con personal encargado en específico del cuarto frío. Su tarea es revisar que todo se encuentre en orden y hacer tres tipos de mantenimiento:
Diario. Se revisan las presiones, temperaturas y amperajes de los equipos
Mensual. Se lavan los serpentines, se revisa el aceite, amperaje y temperaturas; en caso de ser requerido, se cambian fusibles o pastillas dañadas
Trimestral. Se cambian filtros de succión, ya sea de alta o baja, y se realiza un mantenimiento más profundo, que incluye cambio de aceite y carga de refrigerante
En cuanto al conjunto de ductos, el sistema se diseñó de tal manera que fuera necesario el menor número de codos. Dicha consideración busca conseguir una menor caída de presión y contar con una conexión más aerodinámica.
Además de este control en el mantenimiento existe un sofisticado sistema de protección que, en caso de presentarse cualquier fallo de energía, activa una planta de emergencia. Los equipos, asimismo, son monitoreados a distancia y vigilados las 24 horas del día, los 365 días del año.
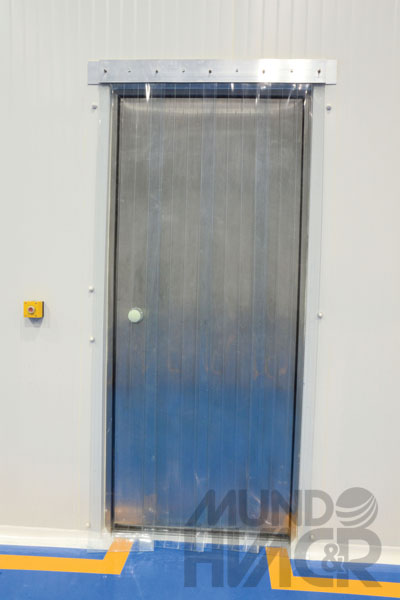
Cámaras frías
Los laboratorios construidos para resguardar las vacunas de influenza H1N1 y algunos otros biológicos están conformados por cuatro cámaras frías de diferentes magnitudes.
Estas cámaras se encargan de la conservación de productos farmacéuticos y cuentan con diversas características.
Todas se encuentran construidas a base de paneles aislados Multypanel, con un espesor de 4 pulgadas y curvas sanitarias para muro-muro, muro-techo y muro-piso. Este tipo de curvas impide la acumulación de residuos en las esquinas, que son inexistentes. El piso es de material resistente al tránsito pesado y libre de emisiones de polvo y partículas, pues el control en la calidad del aire interior es indispensable.
Las cámaras cuentan también con puertas corredizas para entrada de producto y una puerta de paso para personal, las cuales cuentan con cortina de aire y cortina hawaiana, respectivamente. Además, el sistema de calefacción instalado, que se complementa con un cierre hermético, evita la formación de hielo. Para seguridad de los operarios, la puerta paso hombre cuenta con sistema de hombre atrapado que permite la apertura desde el interior.
Las cámaras están diseñadas para operar en rangos de frío establecidos. La temperatura oscila entre 2 y 8 grados centígrados para almacenar vacunas y biológicos para uso humano. Para garantizar este rango y el resguardo cabal de productos, cuentan con un sistema de alerta para alta temperatura (7 °C) y un sistema para alerta por baja temperatura (3 °C).
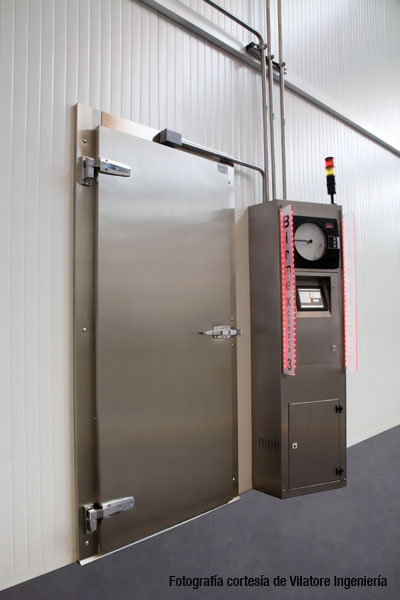
Regularmente, las cámaras trabajan a 4 grados centígrados. Por cada evaporador instalado, hay también una máquina condensadora. En las esquinas de cada condensadora hay una curva sanitaria que evita la proliferación y entrada de microorganismos al interior, que garantiza el cumplimiento con los estrictos niveles de control de partículas.
Sensores tipo PT-100 operan como equipo de control y han demostrado ser muy eficientes en condiciones de bajas temperaturas. El proyecto también incluye un graficador marca Partlow de la gama MRC, que puede ser configurado para operar a diferentes temperaturas de la aplicación, según se requiera.
Los sistemas de refrigeración están conformados por dos grupos de equipos, pues se buscó, además del sistema principal, contar con uno de respaldo para dar mayor seguridad operativa.
Los equipos se encuentran alimentados por las debidas instalaciones de energía eléctrica, suministro de líquido, succión de gas y desagüe, las cuales cumplen las normas de calidad vigentes en su elaboración. Además, el sitio cuenta con un sistema de control y monitoreo desarrollado por Vilatore que optimiza una operación multizona.
Todas las cámaras se sirven de una cortina de aire en su entrada que evita el intercambio de aire frío interior con el caliente del exterior. La red de control de temperatura se complementa con un botón de pánico en el interior, que permite abrir la puerta desde el interior de la cámara en caso de que se cierre y haya algún empleado en el interior.

Las tres cámaras fueron sometidas a un proceso de calificación de protocolos (DQ, IQ, OQ, PQ estudios requeridos por la Comisión Federal para la Protección y Riesgo Sanitario) para poder liberar las cámaras frías y así almacenar las vacunas y los biológicos. Para llevar a cabo estos estudios se llegaron a utilizar hasta 5 mil sensores para comprobar que las temperaturas de operación no tuviesen diferencias mayores a medio grado centígrado de diferencia, en cualquier punto de su interior.
Una de las cámaras, la de proporción media, cuenta con seis máquinas en total, de las cuales normalmente están trabajando tres, mientras que las restantes se mantienen como respaldo. También cuenta con nueve racks de almacenamiento que garantizan el frío necesario para las vacunas que resguardan.
Para cualquier contingencia que se presente, las cámaras cuentan con un sistema de respaldo manual que puede activarlo el personal a cargo. En cuanto a normas de seguridad, los empleados deben portar overol, chamarra térmica, botas de seguridad, casco y guantes antes de ingresar en las cámaras.
Un sistema de alumbrado constituido por lámparas de vapor de sodio ofrece una luminosidad de hasta 400 luxes por metro cuadrado, colocadas a una altura de 1.20 metros. Este tipo de luminarias son ideales para cumplir con las normas de alumbrado que requiere y que establece la STPS.
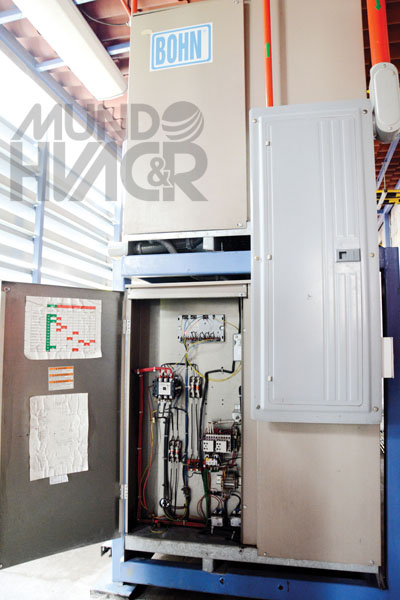
Tablero de control
Cada cámara tiene instalado un tablero de control en el exterior, que permite visualizar el funcionamiento de las tres cámaras. Su diseño es único, ya que se creó con base en las necesidades de las instalaciones.
Cuentan con contraseñas de seguridad para controlar los accesos. Además, cada tablero tiene un sistema auditivo (sirenas) y uno visual (sirenas de colores y pantalla digital).
Dos tipos de notificaciones se emiten mediante el tablero: alarma y alerta. Las alertas se activan cuando el equipo trabaja a una temperatura de entre 3 y 7 grados centígrados. Las alarmas se activan cuando el sistema supera los límites entre 2 y 8 grados.
Además de mostrar las notificaciones en el tablero, se notifica a través de un mensaje de texto a todos los técnicos operadores de las cámaras, dado que ellos cuentan con toda la información acerca del manejo y modo de operación de los sistemas.
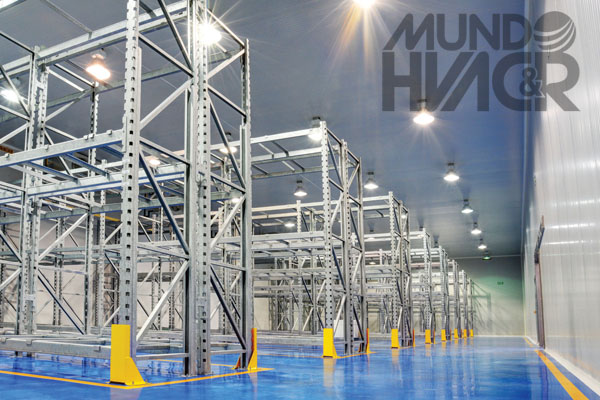
En caso de ausencia de suministro, las cámaras cuentan con un no-break que les permite seguir en funcionamiento.
Cuentan con una gráfica de temperatura que se cambia cada siete días. Ésta resulta de suma importancia, ya que, si se sale del rango, significa que el equipo tiene alguna falla y debe definirse la causa para repararla de inmediato.
Cabe resaltar que dos o tres veces por año se realizan auditorias por parte de la COFEPRIS con el fin de determinar la buena operación de los equipos, de los sistemas de registro y de los procedimientos normalizados de operación para el manejo de la red fría, del mantenimiento de los equipos y del mantenimiento del biológico.
Los laboratorios trabajan diariamente para brindar servicio a toda una nación; un error puede significar grandes pérdidas y riesgos de gran magnitud impermisibles. Por ello, el reto de desarrollar esta instalación requirió la experiencia de expertos en el sector, ofrecida por la firma Vilatore. El ingeniero Pedro Villavicencio resalta que el trabajo tomo un poco más de tiempo; sin embargo, “valió la pena el resultado”.
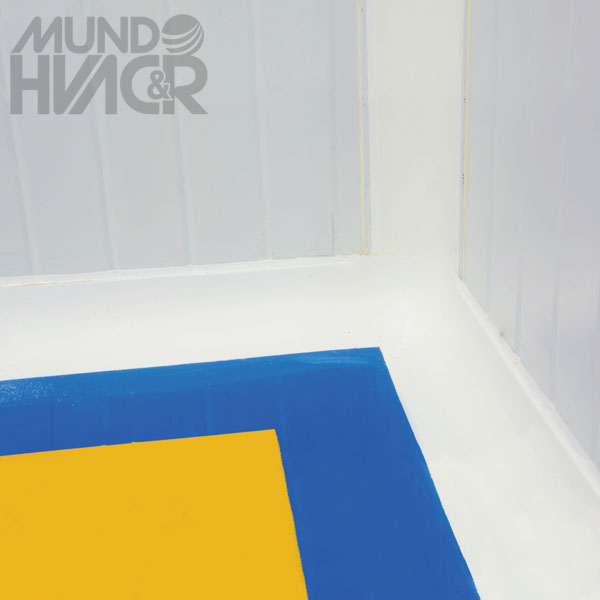
Distribución de los sistemas
Cámara 1
Dimensiones
- 21 metros de largo, por 14.35 metros de ancho y altura de 6.35 metros
El sistema de refrigeración está compuesto por:
- Cuatro unidades evaporadoras marca BOHN, modelo BHG-550
- Cuatro unidades condensadoras marca BOHN, modelo BZT-860M6
Cámara 2
Dimensiones
- Tiene un largo de 36.40 metros, 14.35 metros de ancho y altura de 6.35 metros
El sistema de refrigeración está compuesto por:
- Seis unidades evaporadoras marca BOHN, modelo BHG-450
- Seis unidades condensadoras marca BOHN, modelo BZT-860M6
Cámara 3
Dimensiones
- Tiene un largo 42.70 metros, 14.35 de ancho y 6.35 de alto
El sistema de refrigeración está compuesto por:
- Seis unidades evaporadoras marca BOHN, modelo BHG-640
- Seis unidades condensadoras marca BOHN, modelo BZT-1000M6
Cámara 4
Dimensiones
- 35 metros de largo, 4.70 de ancho y 6.35 de alto
El sistema de refrigeración está compuesto por:
- Dos unidades evaporadoras marca BOHN, modelo BHG-550
- Dos unidades condensadoras marca BOHN, modelo BZT-860M6
———————————————————————————————————————————————–
Agradecemos a los ingenieros Pedro Villavicencio, director de Ingeniería en Vilatore Ingeniería, y Alejandro Villavicencio, gerente de Ingeniería y Proyectos en Vilatore Ingeniería, por su amable colaboración, por la información brindada y por las facilidades para la realización de este reportaje.