Con una capacidad de producción de hasta 300 toneladas por hora y una maquinaria totalmente renovada, la Planta de Asfalto de la Ciudad de México cumple con una doble finalidad: enriquecer la calidad del asfalto al tiempo de reducir la contaminación que implica la producción de este material
Danahé San Juan / Fotografía: Rubén Darío Betancourt
El Departamento de Vulcanología del Instituto de Geofísica de la Universidad Nacional Autónoma de México (UNAM) calcula que hace aproximadamente mil 670 años hizo erupción el volcán Xitle (ombliguito en náhuatl), el cual forma parte del Campo Volcánico de la Sierra Chichinautzin, que a su vez pertenece al Cinturón Volcánico Mexicano.
La lava expulsada por este acontecimiento cubrió ciertas áreas de las actuales demarcaciones Álvaro Obregón, Tlalpan y Coyoacán. En la parte más alta del sudoeste de ésta última delegación están Los Pedregales, cuya superficie se caracteriza por estar recubierta de piedra volcánica y que se convirtió en la base para el desarrollo habitacional de la zona. Como señala el documento La Planta de Asfalto del Distrito Federal: una industria comprometida con el cuidado del medio ambiente, este recurso natural comenzó a ser explotado en 1956, cuando fue creada esta planta, cuyo objetivo era “atender la demanda de mezclas asfálticas para la pavimentación de la red vial que iba surgiendo como consecuencia del crecimiento de la Ciudad de México”.
En los últimos años, este lugar se vio envuelto en una serie de polémicas, debido a temas relacionados con la contaminación, cuidado al medioambiente y demanda de los vecinos de la zona de contar con un espacio de esparcimiento saludable. Ante esta situación, en fechas recientes se realizó una remodelación con el propósito de mejorar la calidad del asfalto y disminuir la contaminación que implica su producción, en beneficio de los habitantes; y como parte del “Programa de Mejoramiento Ambiental”.
La nueva planta tiene una capacidad de producción de 300 toneladas por hora, gracias a las recientes adquisiciones: un equipo productor de mezclas asfálticas y un colector de polvo, con los cuales se podrá reciclar el pavimento que se retire de las vialidades, por primera vez, para así reutilizar hasta 50 por ciento del mismo, a fin de generar nuevo material.
El primero se destaca por una casi nula emisión de contaminantes, debido a su capacidad de controlar las emisiones generadas, con ayuda de cámaras de filtros que capturan el polvo generado durante el proceso de secado. Esto disminuye hasta en 60 por ciento las emisiones de dióxido de carbono (CO2) y dióxido de nitrato (NOX).
Lo anterior permite el cumplimiento de la normativa ambiental vigente en el país, además de las establecidas por la Agencia de Protección Ambiental de Estados Unidos (EPA, por sus siglas en inglés) y a la Agencia Europea de Medio Ambiente (AEMA, por sus siglas en inglés).
El colector de polvos, por su parte, elimina las partículas derivadas de la corriente de escape, con una eficacia de más del 99.5 por ciento.
Otra de las ventajas que se lograrán con el equipo nuevo es la producción de hasta 250 toneladas por hora (60 por ciento más que el equipo anterior) de diversas mezclas asfálticas de la mejor calidad.
Reyes Martínez, director de la Planta de Asfalto de la Ciudad de México, comenta que debido a esta renovación ahora se le denomina planta sustentable, ya que el enfoque principal fue totalmente ambiental. “Actualmente, utilizamos gas natural porque contamina menos; empleamos los finos o derivados del asfalto que ahora ya aprovechamos, también ‘el rechace’ o el producto que no está en condiciones de salir a las calles, el cual estaremos reutilizando, así como el fresado que también podremos reintegrar en un 30 por ciento”.
Además de lo mencionado, otros motivos por los que se llevaron a cabo las modificaciones en la planta fue la contaminación sonora. Para combatir esta problemática se adquirieron quemadores que ahora son más silenciosos. En cuanto a las emisiones contaminantes, antes eran muy pesadas para el aire, pero ahora las mezclas empleadas con temperaturas máximas de 130 ºC conllevan una reducción importante. Otro elemento que se actualizó fue el sistema de filtros para disminuir olores y contaminantes del proceso de secado.
Adicional a estos equipos, las plantas de asfalto también pueden contar con un secador con inclinación ajustable colocado antes de las cribas y con capacidad para secar una cantidad de material pétreo igual o mayor que la capacidad de producción; pirógrafo a la salida del secador para registrar automáticamente la temperatura del material pétreo; equipo para calentar el cemento asfáltico de manera controlada, que garantice la no contaminación del producto y que esté provisto de un termómetro con rango de 20 a 200 °C; una placa de alto rendimiento en el intercambiador de calor utilizado para enfriar el asfalto emulsionado, así como para calentar el agua de enfriamiento para la producción de la mezcla asfáltica; sistema o dispositivo serpentín de calefacción para calentar la emulsión, cuando se trate de plantas de emulsión asfáltica; controles de temperatura; entre otras.
Esta planta de asfalto posee también un compresor de aire de unidad directa de servicio industrial, con múltiples configuraciones que optimizan sus operaciones y garantizan el mejor servicio.
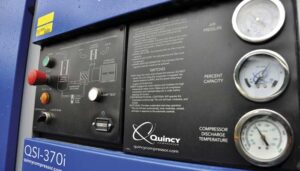
Producción asfáltica
El proceso de producción de la planta asfáltica de Coyoacán consiste en ingresar el material pétreo a los calentadores, con ayuda de las bandas y elevadores. Después, el producto se dirige a la mezcladora y posteriormente se envía a almacenamiento y distribución.
Las tolvas son las alimentadoras de la materia prima, pues en ellas se encuentra el material pétreo que se remite a las cribas vibratorias. Éstas permiten homogeneizar la materia, para después dirigirla al tambor secador-mezclador de doble barril en el que se encuentra una especie de “comal” que conserva la temperatura para secar la mezcla y separar la humedad.
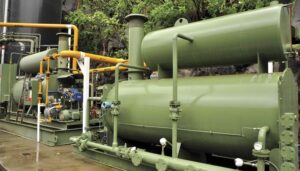
El siguiente paso es una casa de bolsas en la que todas las partículas de polvo que quedan volando se filtran con un movimiento de sacudido, para que en vez de desperdiciarlas se regresen, a través de una espiral, al sistema de tambores, a fin de aprovechar el material. Luego, con un elevador de rastras el material se lleva a los silos de almacenamiento, donde se pueden mantener 600 toneladas de asfalto hasta por 3 días, pero no más, para que se mantenga su óptima calidad. Finalmente, se realiza la carga de asfalto a 150 ºC en los camiones.
Flujo de producción del asfalto
- Recepción de material pétreo virgen
- Recepción de material reciclado
- Traslado de material pétreo a criba vibratoria
- La criba vibratoria separa los sobretamaños del material pétreo
- Traslado del material cribado al tambor secador-mezclador
- Recepción y proceso de secado del material en la cámara interior del tambor secador-mezclador
- Se almacenan los finos y se agregan al tambor secador-mezclador en caso de ser necesario
- Se guarda AC-20 y se agrega al tambor secador-mezclador para realizar la mezcla asfáltica
- Proceso de mezclado en la cámara exterior del tambor secador-mezclador
- Se almacenan los finos que se generan durante el proceso de secado y mezclado evitando que salgan al medioambiente, reincorporándolos al proceso de producción de mezcla asfáltica
- Se eleva la mezcla asfáltica a los silos de almacenamiento
- Almacenamiento de mezcla asfáltica
Existen diferentes tipos de asfalto, de los cuales sobresalen dos:
Mezclas asfálticas en caliente. Como su nombre lo indica, este tipo de asfalto requiere de importantes niveles de temperatura para facilitar su elaboración, vaciado, extendido y compactado. Esta mezcla se realiza por medio de un proceso de dosificación, durante el cual se van incorporando los diferentes materiales que se requieren de la mezcla en frío.
Mientras se realiza el anterior paso, también se aplica el mezclado, pero se debe tener un cuidado especial en la aplicación del aire de combustión y la cantidad de aceite que se utilice. Posteriormente, los elementos se someten a secado para retirar la humedad, mientras se aplica temperatura de entre los 130 a los 150 °C, de manera controlada, para evitar que la mezcla no sea de buena calidad. La importancia de la aplicación de calor radica en que de ella depende la flexibilidad y facilidad para que el asfalto se pueda verter, extender y compactar, pues en cuanto se endurece, ya no es posible manipularlo.
Finalmente, la mezcla se almacena hasta que llegue el momento de descargar el material en un camión, lo cual debe realizarse lo más rápido posible. El resultado de este procedimiento es de gran utilidad para aplicaciones en carreteras y pistas de aterrizaje en aeropuertos.
Mezclas asfálticas en frío. Esta mezca se puede llevar a cabo de dos maneras: una consiste en la preparación de una emulsión y fabricación de la mezcla. Lo primero que se debe hacer es calentar el agua; después se añade el emulgente para provocar una reacción emulsificante; luego, se incorporan los aditivos, y finalmente se agrega el asfalto a una temperatura alta. A continuación, se esparce en una solución, a fin de conseguir la emulsión asfáltica lista para almacenamiento.
La segunda precisa la incorporación, a teperatura ambiente, de los agregados fríos a la emulsión, con ayuda de una mezcladora. El resultado se almacena y puede mantenerse un tiempo considerable en un silo. Esta mezcla es perfecta para conservación, preservación o remodelación de las carreteras urbanas.
Cuidados y energía
El mantenimiento se realiza una vez al año, durante dos o tres fines de semana. Las empresas que se contratan para esta labor hacen el cambio de aceites pesados, principalmente. Las operaciones de la planta no se ven afectadas porque las áreas de mantenimiento y funcionamiento son programadas para que sólo se reduzca la capacidad de producción, sin que esto implique detener la operación por completo de la planta. Este mantenimiento también contribuye al cuidado ambiental, ya que al efectuarlo se garantiza un óptimo funcionamiento y la reducción de los contaminantes.
El sistema de energía que abastece la planta posee trasformadores y subestaciones que derivan la energía a utilizar en los diferentes sistemas. También hay tableros de distribución automatizados que regulan la corriente a los equipos de extracción de polvo, tambores y demás equipos, los cuales utilizan 110 volts. En caso de que ocurra una falla, los tableros emiten alertas que son atendidas por los encargados de cada área, quienes primero dan aviso a la central y después proceden a revisar la falla. Cuando las alarmas se activan, las operaciones se desactivan para poder corregir la falla; en caso de que el panel falle, se tienen paradores de emergencias manuales que detienen los procesos. “El tema aquí son las presiones, las temperaturas y, lo más importante de todo, en dónde se encuentra el material para evitar que se atasquen las bandas de distribución y/o que ocurra alguna explosión o incendio; para esto nuestros operadores cuentan con una amplia experiencia y capacitación”, detalla el Director de la Planta.
Cabe destacar que a partir de la modernización de la planta, de las 18 hectáreas que la conforman, entre 10 y 12 se han destinado a la creación de un espacio verde que beneficie a los vecinos de la zona y al planeta, al tiempo que se recupera la identidad del Pedregal de San Ángel con un espacio escultórico.
Lo anterior, para demostrar que la industria y la naturaleza pueden convivir en un mismo tiempo y espacio. La producción de asfalto es una necesidad que facilita diversos ámbitos de la vida humana, gracias a que con este material es posible construir infraestructura vial para comunicar a las personas, comunidades y ciudades, además de facilitar la movilidad de bienes, servicios y productos.
Equipos que conforman la Planta de Asfalto de la Ciudad de México
Tolvas receptoras de material pétreo: estos equipos cuentan con una estructura resistente diseñada para enfriar el líquido contenido
- Criba vibratoria de 2 camas: clasifica el material pétreo y debe contar con la capacidad para mantenerlo siempre en las tolvas para la mezcla asfáltica
- Tambor secador-mezclador de doble barril: este tipo de equipos posee un sistema de calefacción uniforme, eficiente uso de energía, material aislante y acero inoxidable para evitar la pérdida de calor
- Colector de finos
- Silo de almacenamiento que protege de la humedad a los finos de aportación. Está integrado por un sistema de dosificación ajustable y operación independiente a la del sistema utilizado para el resto de los materiales pétreos
- Tolvas receptoras de material reciclado
- Calentadores de aceite térmico: pueden tener sistemas de calentamiento con quemador de fuego directo, con capacidad calorífica desde 800,000 hasta 10,000,000 btu/hr
- Tanques de almacenamiento de clasificación AC-20, según la viscosidad dinámica a 60 °C del material (capacidad de 100,000 lts)
- Elevadores de rastras
- Silos de almacenamiento de producto terminado (capacidad de 200 toneladas por silo)